Beim Auslegen von Nietverbindungen hat ein Konstrukteur neben den einschlägigen Normen auch Regeln bezüglich Niettyp und Nietgröße, Werkstoff und kompatiblen Materialkombinationen zu berücksichtigen. Dieser Beitrag gibt aus Konstruktionssicht einen Überblick über das Nieten als Verbindungstechnik sowie seine Vor- und Nachteile gegenüber anderen Verfahren. Unter anderem beantwortet er die Frage, wie die (mögliche) Lösbarkeit zu Wartungs- und Sanierungszwecken konstruktive Entscheidungen beeinflussen kann.
Thomas Preuß, Fachjournalist in Königswinter, turmpresse.de
Zu den Grundlagen der Verbindungstechnik sind von Thomas Preuß erschienen:
-
- Brauchen wir in zehn Jahren noch Verbindungstechniken?
- Schweißen, schrauben oder nieten?
Welche Verbindungstechnik sollte ein Konstrukteur wählen? - Wie ein Konstrukteur bei der Planung einer Schweißkonstruktion vorgehen sollte
- Schrauben und Schraubverbindungen – das sollte der Konstrukteur wissen
- Wie man Nietverbindungen auslegt und was ein Konstrukteur dabei unbedingt vermeiden muss
- Welche Normen und Richtlinien beim Nieten gelten
Inhaltsverzeichnis
1. Konstruktionsregel Nummer eins für Nietverbindungen: den richtigen Werkstoff wählen
2. Wie funktioniert das Nieten und was ist seine wesentliche Eigenschaft gegenüber anderen Verbindungstechniken?
3. Beim Stanznieten muss nicht vorgebohrt oder vorgestanzt werden
4. Kaltniet- und Warmnietverfahren
5. Nietverbindungen sind „bedingt lösbar“
6. Lösbarkeit zu Wartungs- und Sanierungszwecken beeinflusst konstruktive Entscheidungen
7. Vorteile des Nietens
8. Niet-Anwendungen im Flugzeug- und Automobilbau kombinieren Festigkeit mit Leichtigkeit
9. Nachteile des Nietens und von Nietverbindungen
10. Nicht-kompatible Werkstoffkombinationen unbedingt vermeiden
11. Was ein Konstrukteur bei der Auslegung einer Nietverbindung (noch) beachten sollte
12. Niettypen: Vollniete, Hohlniete und Blindniete
13. Die Kopfformen von Nieten
14. Nietgröße: Länge und Durchmesser richtig auslegen
15. Sinnvolle geometrische Anordnung führt zu besserer Lastverteilung
Starten wir mit der sprachlichen Klärung: Der Niet; die Niete.
Die Niete; die Nieten. Wenn Sie über „die Niete(n)“ mehr erfahren möchten, gehen Sie bitte auf der nächsten Kirmes an eine Losbude und versuchen Ihr Glück.
Wenn Sie an konstruktiven Einlassungen zur Verbindungstechnik des Nietens interessiert sind, bleiben Sie dran. Die Fügeelemente heißen im Singular „der Niet“, im Plural „die Niete“. Jedenfalls im Hochdeutschen.
Tragisch kann es werden, wenn Niete „Nieten“ sind und ihre Aufgabe nicht erfüllen können, weil sie nicht den Vorgaben der Konstrukteure entsprachen – zum Beispiel aus einem weniger festen Werkstoff hergestellt wurden als vorgesehen. So haben Wissenschaftler in Archiven der Herstellerwerft der Titanic Hinweise darauf gefunden, dass ein Teil der 3 Millionen Niete, die das aus 2000 Stahlplatten erbaute Schiff zusammenhalten sollten, minderwertig waren. Sie könnten den Untergang des Ozeanriesen auf seiner Jungfernfahrt 1912 mindestens beschleunigt haben.
Zwar seien bei der Titanic mindestens an der Rumpfmitte, wo die größten Belastungen erwartet wurden, durchaus die konstruktiv vorgesehenen Stahlnieten verwendet worden. Doch am Bug, wo der Eisberg das Schiff traf, sowie am Heck seien Eisennieten zum Einsatz gekommen. Dies legte eine Analyse des Metalls nahe: Es sei von kleinen Schlackebrocken durchsetzt gewesen. Der glasige Rückstand entsteht bei der Verhüttung und kann Niete brüchig machen. Die Werft wies alle Schuld von sich, doch angesichts der seinerzeit strapazierten Lieferketten, die zur Beschaffung von Nieten auch bei kleineren – heute würde man sagen: nicht zertifizierten – Herstellern führte, scheint der Einsatz minderwertiger Niete belegt.
Konstruktionsregel Nummer eins für Nietverbindungen: den richtigen Werkstoff wählen
Mit Blick auf das Unglück können wir hier Konstruktionsregel Nummer eins für Nietverbindungen unterbringen: Wähle Sie das Material immer so, dass die Niete gleich hart oder härter sind als die Bauteile, die sie zusammenhalten sollen. Kann vielleicht mal Leben retten. Grundsätzlich sollte der Niet aus einem ähnlichen Werkstoff bestehen wie mindestens eine der zu fügenden Komponenten, um elektrochemische Korrosion zu vermeiden. Gängig sind Stahl und Edelstahl, Aluminium, Kupfer und Messing.
Der Anteil nicht ausreichend belastbarer Niete am Titanic-Unglück – und welchen Zeitvorsprung stählerne Niete bei dem Untergang gebracht hätten – wird vermutlich nie bis ins Letzte geklärt werden können. Klar scheint: Das Wasser konnte sich dadurch im Inneren des Schiffes wohl schneller ausbreiten. Andererseits: Ohne die Kollision mit dem Eisberg wäre die Titanic gar nicht gesunken. Hätte, hätte, Fahrradkette.
Umso wichtiger jedenfalls, dass die Konstrukteure dieser Welt bei der Auslegung von Nietverbindungen wissen, wie sie vorgehen müssen, und die Einkäufer und Produktionsverantwortlichen sich an deren konstruktive Spezifikationen halten – insbesondere in sicherheitskritischen Anwendungen wie dem Flugzeug- und Schiffsbau oder der Errichtung von Brücken und Hochhäusern. Übrigens wurden auch die Golden Gate Bridge und das Empire State Building mit Millionen von Nieten erbaut. Beim einstmals höchsten Gebäude der Welt sind genietete Verbindungen ein wesentlicher Bestandteil der Stahlrahmenstruktur.
Wie funktioniert das Nieten und was ist seine wesentliche Eigenschaft gegenüber anderen Verbindungstechniken?
Beim Nieten werden zwei oder mehr Werkstücke miteinander verbunden, indem das Fügeelement, der Niet, durch die Bauteile gesteckt wird. Auf der einen Seite sitzt der „Setzkopf“ des Niets auf dem oberen Bauteil auf; auf der gegenüberliegenden Seite wird sein Schaftende mit einem Werkzeug (einem Niethammer, einer Nietpresse oder Nietzange) verformt oder verpresst. Dadurch entsteht auf dieser Seite der „Schließkopf“.
Zuvor müssen außer beim Stanznieten alle beteiligten Werkstücke, die miteinander verbunden werden sollen, durchbohrt werden. Dabei ist wichtig, dass das Bohrloch minimal größer ist als der Durchmesser des Niets. Dieser hält anschließend die einzelnen Komponenten zusammen und bildet normalerweise eine dauerhafte, formschlüssige, mechanisch feste Verbindung.
Beim Stanznieten muss nicht vorgebohrt oder vorgestanzt werden
Beim Stanznieten werden die Komponenten durch Einspreizen eines Hilfsfügeteils (z. B. Halbhohl- oder Vollstanzniet) miteinander verbunden. Im Gegensatz zu anderen Niettypen benötigen Stanznieten keine vorgebohrten oder vorgestanzten Löcher. Die Geometrie erlaubt es dem Niet, die zu verbindenden Bauteile zu durchstoßen. Via Stanznieten können gas- und wasserdichte Verbindungen hergestellt werden.
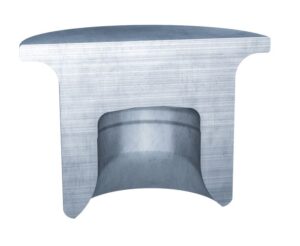
Bild: Atlas Copco
Nietverbindungen sind allgemein sehr hitzebeständig und halten hohen Belastungen und Vibrationen gut stand, womit sie gleich mehrere Vorteile gegenüber geklebten und geschraubten Verbindungen haben.
Im Gegensatz zum Schweißen wiederum entsteht beim Nieten keine zu hohe Wärme – selbst beim Warmnieten nur bedingt – die die Werkstücke verformen oder ihre Materialeigenschaften verändern könnte.
Besonders die Widerstandsfähigkeit gegen Schwingungen und hohe Temperaturen sind Gründe, weshalb die Niettechnik zum Beispiel in vielen (historischen) Brückenkonstruktionen eingesetzt wurde und heute noch in Flugzeugen, Lokomotiven oder Bussen, in Turbinen oder Hochtemperaturanlagen ein Spielfeld findet. Übrigens werden auch Gürtel, Taschen und Ledersättel für Fahrräder noch genietet; das aber nur nebenbei.
Kaltniet- und Warmnietverfahren
Beim Nieten unterscheiden wir das Kalt- und das Warmnietverfahren. Das Kaltnieten wird weitaus häufiger angewandt. Der Vorteil ist, dass die Niete nicht erwärmt werden müssen und sich auch hitzeempfindliche Stoffe fügen lassen, etwa Aluminium oder Kunststoffe. Das schützt ihre Oberflächen, und der Prozess ist bezüglich Druck und Geschwindigkeit besser zu kontrollieren. Das Kaltnieten ist besonders dann interessant, wenn thermische, stoffschlüssige Fügeverfahren, wie Lichtbogenschweißen, Löten oder Kleben, wegen der Materialeigenschaften nicht das Mittel der Wahl sind.
Der Vorteil beim Warmnieten ist dagegen, dass durch das Zusammenziehen der Niete nach der Abkühlung zusätzliche Klemmkraft entsteht. Die Vorspannkraft wird gleichmäßiger verteilt, die Verbindung dadurch stabiler. Allerdings hat der Nietschaft dann weniger Kontakt zur Bohrung. Dies stellt aber kein Problem dar, weil diese Nietverbindungen auf Zug belastet werden.
Im Vergleich zum Schweißen werden die Bauteile beim Warmnieten erheblich weniger mit Wärme beaufschlagt, wodurch sich die Komponenten weniger verziehen. Dagegen entsteht in den Flächen entlang einer Schweißnaht die sogenannte „Wärmeeinflusszone“, in der sich die Materialeigenschaften, insbesondere die Streckgrenze des Metalls, ungünstig verändern können. Dies passiert beim Warmnieten nicht.
Nietverbindungen sind „bedingt lösbar“
Während beim Schweißen und Kleben die einzelnen Strukturkomponenten unlösbar und beim Schrauben in der Regel lösbar miteinander verbunden werden, sind Nietverbindungen „bedingt lösbar“. Das bedeutet, dass zum Trennen zwar das Verbindungselement, in diesem Falle also der Niet, zerstört werden muss; die Bauteile selbst bleiben dabei aber intakt. Oft ist vielleicht ein Blech der Konstruktion beschädigt, so dass es (zum Beispiel) durch Abschlagen der Nietköpfe leicht ausgetauscht werden kann.
Die Lösbarkeit oder Nicht-Lösbarkeit ist eine der wesentlichen Eigenschaften einer Verbindung. Ihre Notwendigkeit muss daher am Anfang des Auswahlprozesses für den kompletten Lebenszyklus des Produktes überprüft werden. Unter anderem hat die Lösbarkeit entscheidenden Einfluss auf spätere Wartungsarbeiten sowie auf die Reparatur- und Recyclingfähigkeit, die im Übrigen bei Schraubverbindungen noch eher gegeben ist.
Lösbarkeit zu Wartungs- und Sanierungszwecken beeinflusst konstruktive Entscheidungen
Bei der Auslegung von Nietverbindungen sollten Konstrukteure daher die Lösbarkeit – und die Einflussfaktoren auf diese – berücksichtigen, wenn an der jeweiligen Konstruktion später einmal Wartungsarbeiten oder Reparaturen zu erwarten sind. Dies kann die Auswahl des geeigneten Niettyps, die Montage der Niete und andere konstruktiven Entscheidungen beeinflussen.
So werden an Flugzeugen aufgrund strenger Wartungsanforderungen und der Notwendigkeit, bestimmte Komponenten regelmäßig auszutauschen, Nietverbindungen am Rumpf sowie an den Flügelstrukturen regelmäßig gelöst und wieder hergestellt. Ähnlich verhält es sich mit Schienenfahrzeugen und Gleisen, aber auch an Schiffen, Brückenkonstruktionen oder historischen Gebäuden. So soll bei deren Restaurierung oft die traditionelle Bauweise und Optik erhalten bleiben. Ein Beispiel ist die aus zahlreichen Nietverbindungen konstruierte Werther Brücke, über die die Wuppertaler Schwebebahn fährt. Sie wurde vor gut zehn Jahren aufwendig saniert.
Wie gut eine Nietverbindung lösbar ist, hängt von verschiedenen Faktoren ab. So sind einige Niettypen, wie Blindnieten, schwieriger zu entfernen als andere, weil sie spezielle Werkzeuge erfordern. Auch der Werkstoff, aus dem die Niete bestehen, hat einen Einfluss: Wird das Material schnell spröde oder korrodiert leicht, kann dies die Entfernung erschweren. Dies gilt nicht zuletzt auch für die Formen des Nietkopfes und des Nietendes, eine zu hohe Vorspannkraft bei der Montage der Niete sowie eine schlechte Zugänglichkeit zur Verbindung. All diese Faktoren können die Demontage verkomplizieren.
Vorteile des Nietens
Generell eignet sich das Nieten gut für Anwendungen, bei denen Festigkeit, Stabilität, Korrosionsbeständigkeit und Wartungsfreundlichkeit gefragt sind. Mit dem technischen Fortschritt im Bereich der Verbindungstechniken werden heute jedoch viele Konstruktionen lieber geschweißt, geschraubt oder geklebt.
Zum Einsatz kommt das Nieten als bevorzugte Verbindungstechnik heute vor allem noch dann, wenn unterschiedliche Materialien, wie zum Beispiel Aluminium und Stahl, dauerhaft miteinander verbunden werden sollen. Dadurch lassen sich die spezifischen Eigenschaften jeder Komponente nutzen. Das Verfahren an sich beeinflusst den Werkstoff nicht negativ, wie es durch Aufhärtungen (unbeabsichtigte Härtesteigerungen) oder Gefügeumwandlungen beim Schweißen möglich ist. Auch verziehen sich die Bauteile nicht. Moderne Blindnietsysteme ermöglichen sehr schnell herstellbare, kostengünstige Verbindungen für hohe Ansprüche, auch wenn die „Rückseite“ (Schließkopfseite) nicht zugänglich ist.
Niet-Anwendungen im Flugzeug- und Automobilbau kombinieren Festigkeit mit Leichtigkeit
Beispiele für Multi-Material-Anwendungen finden sich unter anderem bei Karosserieteilen in der Automobilfertigung (wenn Stahl- oder Aluminiumbleche mit Kunststoffteilen via Stanznieten verbunden werden) oder im Flugzeugbau: Hier werden etwa Titan, Aluminium oder Verbundwerkstoffe genutzt, um Festigkeit und Leichtigkeit miteinander zu kombinieren. Je nach Anforderungen fällt die Wahl häufig auch auf Komponenten zum Beispiel aus Nickel- und Kupferlegierungen. Nickel ist hochtemperaturbeständig, Kupfer korrosionsbeständig und leitfähig. Beachten Sie immer die mechanischen Anforderungen, die Umgebungsbedingungen, die Betriebstemperaturen und die spezifischen Merkmale der Anwendung, wenn Sie eine Nietverbindung auslegen möchten.
Nachteile des Nietens und von Nietverbindungen
Die Montage dauert vergleichsweise lange, weshalb die Fertigung kostenintensiver ist als das Schweißen. Zudem sind genietete Verbindungen „sperriger“ als geschweißte Verbindungen: Es gibt keine glatten Wände, was zum Beispiel im Behälterbau ungünstig ist und sich auch negativ auf den Kraftfluss auswirkt. Im Druckbehälterbau beispielsweise sind Nietverbindungen vollständig von Schweißverbindungen abgelöst worden, im Stahlbau ganz überwiegend von Schweiß- und Schraubenverbindungen. Von Nachteil ist ebenfalls, dass die Bauteile durch die Nietlöcher geschwächt werden. Dadurch sind größere Querschnitte und allgemein schwerere Konstruktionen erforderlich. Außerdem beeinflusst der Nietvorsprung das ästhetische Erscheinungsbild.
Nicht-kompatible Werkstoffkombinationen unbedingt vermeiden
So verlockend die Kombination der „besten Eigenschaften aus mehreren Welten“ klingt, so umsichtig muss ein Konstrukteur dabei vorgehen. Die kombinierten Werkstoffe müssen miteinander kompatibel sein, um unerwünschte chemische Reaktionen, Korrosion oder mechanische Probleme zu vermeiden. Folgende Unverträglichkeiten sind zu beachten, damit die Verbindung stabil, haltbar und korrosionsbeständig ist:
- Die einzelnen Komponenten müssen grundsätzlich chemisch kompatibel sein, damit sie unter Einfluss von (Luft-)Feuchtigkeit oder in aggressiven Umgebungen nicht unerwünscht miteinander reagieren und die Integrität der Verbindung beeinträchtigen. So unterscheiden sich Metalle oft bezüglich ihrer chemischen Eigenschaften und ihres Korrosionsverhaltens. Die Folge kann eine elektrochemische Korrosion sein, die die Verbindung schwächen kann. Führen Sie daher zum Beispiel Kupfer nicht direkt mit Aluminium zusammen.
- Wenn Werkstücke mit stark unterschiedlichen Härten genietet werden, kann es zu lokaler Verformung oder Rissbildung kommen. Bauteile und Niete sollten daher ähnliche mechanische Eigenschaften haben.
- Beschichtungen, wie Lacke, Farben oder andere Oberflächenbehandlungen, sollten kompatibel sein, um Haftungsprobleme oder chemische Reaktionen zu vermeiden.
- Materialien mit stark unterschiedlichen Wärmeausdehnungskoeffizienten können Spannungen in der Nietverbindung verursachen.
- Schließlich kann auch das Vernieten von thermoplastischen Kunststoffen mit Metallen problematisch sein, da – im Falle des Warmnietens – die Wärme des Nietprozesses den Kunststoff schmelzen könnte. Hier ist das Kaltnieten die bessere Wahl; vielleicht möchten Sie in solchen Fällen aber ohnehin lieber schrauben oder kleben.
Was ein Konstrukteur bei der Auslegung einer Nietverbindung (noch) beachten sollte
Nietverbindungen müssen eine definierte Festigkeit, Stabilität und Zuverlässigkeit aufweisen. Um diese zu erreichen, müssen Konstrukteure alle auftretenden Kräfte berücksichtigen, ferner die Werkstoffe der Bauteilen und Niete sowie deren Typ, Größe und Anordnung. Hierzu sollten die in diversen Normen verankerten Produktspezifikationen und Berechnungsverfahren zu Rate gezogen werden, die wir für Sie in einem weiteren Beitrag zusammengestellt haben.
Niettypen: Vollniete, Hohlniete und Blindniete
Niettyp und Nietgröße müssen zur Anwendung passen. Nach der Ausführung des Nietschaftes unterscheidet man Vollniete mit vollem Schaft, Hohl- und Rohrniete mit hohlem Schaft, Halbhohlniete mit angebohrtem Schaft, Nietzapfen und Blindniete.
Vollniete werden nach der Form ihres Setzkopfes benannt (Halbrundniete, Flachsenkniete). Sie sind im Stahlbau – wie an Industriehallen, Hochhäusern, Brücken oder Schiffen – traditionell weit verbreitet. Das Fügeverfahren nennt sich entsprechend „Vollnieten“.
Mit Hohl- oder Halbhohlnieten werden, insbesondere im Automobilbau, Kunststoffe, Aluminium- und Stahlbleche auf dem Wege des Stanznietens miteinander verbunden. Dabei gibt es zwei wichtige Grundregeln: Der Nietprozess sollte vom härteren ins weichere Material stattfinden und von der dünneren in die dickere Materialschicht verlaufen. Die unterste Lage sollte mindestens ein Drittel der Gesamtdicke der Verbindung ausmachen.
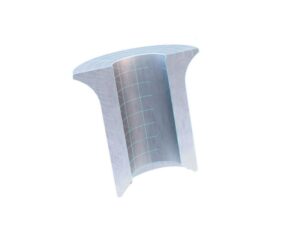
Bild: Atlas Copco
Blindniete haben gegenüber Vollnieten den Vorteil, dass sie auch bei Konstruktionen verwendet werden können, die nur einseitig zugänglich sind. Das Fügeverfahren heißt „Blindnieten“. Die Fügeelemente bestehen aus einer Blindniethülse und einem Nietdorn, der im hohlen Schaft des Niets mitgeführt wird und unten etwas über den Rand hinausragt. Er wird nach dem Setzen zurückgezogen und verformt dabei das Schaftende. Dadurch wird der Niet auf der Gegenseite verschlossen, ohne dass diese Seite zugänglich sein muss.
Die Kopfformen von Nieten
Der Halbrundkopf ist die gebräuchlichste Kopfform (DIN 660, DIN 124) bei Vollnieten; er wird gelegentlich noch im Stahlbau eingesetzt. Senkniete (DIN 661, DIN 302) sind ebenfalls Vollniete und werden überall dort eingesetzt, wo der Nietkopf nicht vorstehen darf. Die Verbindung ist jedoch nicht so belastbar. Vereinzelt sind auch Flachrund- und Flachsenkköpfe sowie weitere Varianten zu finden. Vollniete werden insgesamt jedoch immer weniger eingesetzt; stattdessen wird lieber geschweißt oder geschraubt. Im Gegensatz dazu sind Hohlniete nach wie vor gefragt. Darunter erfahren vor allem die Blindniete eine hohe Nachfrage, weil sie relativ einfach zu verarbeiten sind.
Nietgröße: Länge und Durchmesser richtig auslegen
Um die Abmessungen eines Niets abzuschätzen, sind folgende Faustregeln hilfreich:
- Der Niet sollte etwa so lang sein wie die Summe der Dicke aller genieteten Materialien plus das 1,5-fache des Niet-Durchmessers. Ein zu kleiner Niet kann durch die Bauteile gezogen werden, ein zu dünner Nietschaft unter Druck leicht abscheren.
- Der Durchmesser des Niets sollte mindestens dreimal so breit sein wie die Dicke des dicksten Bleches, das genietet wird. In Bezug auf Blindnieten finden sich auch Empfehlungen von „mindestens so breit wie das dickste Material“.
- Der Durchmesser des Gegenkopfes der Nietverbindung muss größer sein als der 1,4-fache Durchmesser des Schaftes, und die Höhe des Gegenkopfes muss größer sein als der 0,3-fache Durchmesser des Schaftes.
Druckluft-Nietwerkzeuge von Chicago Pneumatic für die Luft- und Raumfahrt
Sinnvolle geometrische Anordnung führt zu besserer Lastverteilung
Um eine gute Lastverteilung zu erzielen und die Stabilität der Verbindung zu erhöhen, ist eine sinnvolle Anordnung der Niete unerlässlich. So müssen zum Beispiel die Anzahl der Niete, ihre Positionen, der Abstand zwischen ihnen sowie zu den Bauteilkanten sorgfältig bestimmt werden.
Doch wann kann die Anordnung der Niete als sinnvoll bezeichnet werden? Die Antwort hängt unter anderem von der Geometrie der zu verbindenden Werkstücke ab, von den künftigen Belastungen sowie den spezifischen Anforderungen der Anwendung. Grundsätzlich sollten die Niete so angeordnet werden, dass die Belastung gleichmäßig über den gesamten gefügten Bereich der Konstruktion verteilt wird, um eine optimale Festigkeit zu erreichen. Platzieren Sie die Niete entweder symmetrisch, also in regelmäßigen Abständen, oder in Bereichen mit höheren Belastungen. Auch sollten Sie dabei Spannungskonzentrationen vermeiden, die zu lokaler Überlastung oder Versagen führen könnten. In einigen Fällen kann es sinnvoll oder erforderlich sein, mehrere Reihen von Nietverbindungen zu setzen. Dann sollen aber die Niete der oberen Reihe nicht über den Nieten der unteren Reihe liegen, da dies die strukturelle Integrität beeinträchtigen könnte.
Ein ausreichender Abstand zu den Bauteilrändern ist wichtig, um sicherzustellen, dass die Niete eine stabile und zuverlässige Verbindung bilden können. Für eine größtmögliche Festigkeit der Verbindung sollte der Abstand von der Mittelachse der Niete zur Kante des Werkstückes mindestens den doppelten Hülsendurchmesser betragen. Die genauen Abstände hängen von den Abmessungen der Werkstücke und den verwendeten Nieten ab.
Nicht zuletzt sollten die Nietstellen aus Gründen der Wartungsfreundlichkeit leicht zugänglich sein, ohne die gesamte Struktur zu beeinträchtigen.