Welche Aspekte beeinflussen – neben den physikalisch wirkenden Kräften – den Schraubprozess und damit die Qualität einer Schraubverbindung? Welche Schraubmontage-Verfahren haben sich in der industriellen Fertigung etabliert und worin unterscheiden sie sich? Und nicht zuletzt: Welche Eigenschaften von Verbindungselementen sollten Sie besonders beachten, wenn Sie einen Montageprozess automatisieren möchten? Diese Fragen beantwortet der folgende Beitrag.
Zu den Grundlagen der Schraubtechnik sind in dieser Serie erschienen:
- Teil 1: Was ein Konstrukteur über Schrauben, Muttern und Gewinde wissen muss
- Teil 2: Normen, Richtlinien und Auslegung einer Schraubverbindung
- Teil 3: Schrauben – Werkstoffe, Herstellung und Prüfbescheinigungen
- Teil 4: Schraubmontage: Gängige Verfahren und Tipps zur Automatisierung
- Teil 5: Schraube locker? Nicht, wenn Sie diese Sicherungsmaßnahmen treffen
- Teil 6: Dichtungstechnik: Bohrungen und Wartungsöffnungen sicher abdichten und verschließen
- Teil 7: Aktiver und passiver Korrosionsschutz für Verbindungselemente
Inhaltsverzeichnis
1. Drehmoment als Hilfsgröße für die Vorspannkraft
2. Je nach Reibung wird nur wenig Drehmoment in Vorspannkraft umgesetzt
3. Qualität einer Schraubverbindung hängt ab von: Konstruktion, Fertigung, Bauteil, Setzverlusten und Schraubsystem
4. Klassifizierung von Schraubstellen durch Risikoabschätzung ist unerlässlich
5. Fertigung nach dem Stand von Wissenschaft und Technik
6. Die wichtigsten Verfahren in der Schraubmontage
7. Diese Faktoren beeinflussen die Automatisierung von Schraubmontageprozessen
Damit eine Schraubenverbindung dauerhaft hält, muss sie konstruktiv korrekt ausgelegt und bei der Montage gemäß den Vorgaben angezogen werden. Maßgeblich für die Betriebssicherheit ist die zuvor errechnete und bei der Montage aufgebrachte Montagevorspannkraft.
Drehmoment als Hilfsgröße für die Vorspannkraft
Die Vorspannkraft ist als physikalische Größe bei den meisten Schraubenverbindungen nicht direkt messbar. Anders das Montagedrehmoment: Es ist relativ einfach zu messen und verhält sich direkt proportional zur Vorspannkraft. Daher wird das Drehmoment häufig als Hilfsgröße für die Vorspannkraft verwendet (Bild 1).
Die Vorspannkraft wird erzeugt, indem bei der Montage ein Drehmoment von außen in die Verbindung eingebracht wird. Um dabei eine möglichst exakt definierte Klemmung der zu verbindenden Komponenten zu erzielen, kann neben dem Drehmoment als gängigster Hilfsgröße auch die Längenänderung der Schraube als Maß für die Vorspannkraft herangezogen werden; sie ist aber aufwendiger zu messen.
Das Montagedrehmoment sollte so gewählt werden, dass die resultierende Klemmkraft im Betrieb zu einem reinen Reibschluss zwischen den Bauteilen führt und gleichzeitig keines der verspannten Elemente überlastet wird.
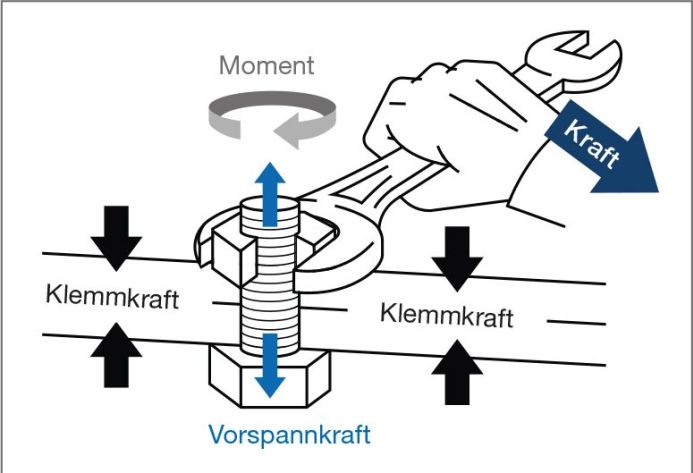
Bild: Böllhoff
Je nach Reibung wird nur wenig Drehmoment
in Vorspannkraft umgesetzt
Ein weiterer wichtiger Faktor, der die Funktionstüchtigkeit einer Schraubenverbindung beeinflusst, ist die Reibung. Daher ist auch sie bei der Montage zu berücksichtigen. So werden zum Beispiel bei einem Reibungswert von µ = 0,2 nur 10 % des von außen aufgebrachten Drehmoments in Vorspannkraft umgesetzt. Die Reibung wird unter anderem vom verwendeten Schmiermittel bestimmt, von der Oberfläche und der Beschichtung, der Bauteilpassung, ferner von Umgebungsbedingungen wie der Temperatur oder der Luftfeuchtigkeit, aber auch von der Kopfauflage der Schraube und der Anzugsgeschwindigkeit.
Qualität einer Schraubverbindung hängt ab von:
Konstruktion, Fertigung, Bauteil, Setzverlusten und Schraubsystem
Daneben beeinflussen folgende weitere Faktoren den Montageprozess und damit die Qualität der Schraubverbindung:
- Die Konstruktion: Wichtige Parameter sind Berechnung und Zeichnungsvorgaben, Normeneinhaltung, Dimensionierung, vorgegebenes Anzugsverfahren, thermische Beständigkeit und Festigkeitsverhältnisse.
- Die Fertigung: Hier wirken sich die Art der Schraubenzuführung und der Einfädelprozess, die Fixierung des Bauteils und des Einschraubwerkzeugs, die Sauberkeit am Arbeitsplatz, die Systematik der Fehlererkennung und der Nacharbeit sowie die Zeitvorgaben aus auf die Qualität der Verbindung aus.
- Das Bauteil selbst nimmt Einfluss durch seine Geometrie und Maßhaltigkeit, die Festigkeit, etwaige Walz- oder Materialfehler, Risse und Oberflächengüte.
- Des Weiteren können Setzverluste entstehen, und zwar durch die Fügemethodik und Anzugsgeschwindigkeit, etwaige Dichtelemente, Lacke und Beschichtungen, Luftspalte, aufgebrachtes Wachs oder ein ungünstiges Klemmlängenverhältnis.
- Schließlich spielt das verwendete Schraubwerkzeug oder Schraubsystem eine große Rolle. Genauigkeit, Zuverlässigkeit und Prozesssicherheit stehen hier ganz oben auf der Liste der Einflussfaktoren. Diese wiederum hängen von der Art des Antriebs bzw. der Arbeitsweise ab (zum Beispiel Druckluft versus gesteuerte Schraubtechnik; manuelle Montage versus halb- oder vollautomatisches Schraubsystem). Auch die Einhaltung der einschlägigen Normen, die verwendete Messmethodik und vieles mehr wirken sich auf den Montageprozess und das Ergebnis aus.
Eine systematische Darstellung aller wesentlichen Einflussgrößen finden Sie unter anderem in der VDI/VDE-MT 2637-1, in der es um die Qualifikation von Mitarbeitern und Führungskräften im Bereich der Schraubtechnik geht.
Was ein Konstrukteur über Schrauben, Muttern und Gewinde wissen muss
Klassifizierung von Schraubstellen
durch Risikoabschätzung ist unerlässlich
All diese Punkte sollten Konstrukteure genauso wie Betriebsleiter und andere für die Produktion Verantwortliche im Kopf haben, wenn sie sich für eine bestimmtes Montageverfahren oder Schraubsystem entscheiden müssen. Abgesehen davon, dass die Entscheidung immer auch von der Losgröße und den Taktzeiten an dem geplanten Arbeitsplatz oder der Montagelinie abhängt, ist aus Gründen der Produkthaftung heute eine Klassifizierung der eigenen Schraubstellen unerlässlich – wenn man vor Rückrufen und Imageschäden sicher sein, dabei aber möglichst wirtschaftlich produzieren möchte.
Einschlägig sind hier diverse Regelwerke wie die DIN 25201 für den Schienenfahrzeugbau sowie die VDI/VDE 2862, Blatt 1 und 2, für die Automobilindustrie und den Allgemeinen Maschinen- und Anlagenbau. Dort wird jeweils beschrieben, dass es den Produktverantwortlichen obliegt, für jede Schraubstelle eine Risikoabschätzung vorzunehmen, und diese wie folgt zu klassifizieren:
- Kategorie A: Risiko für Leib und Leben sowie die Umwelt („sicherheitskritisch“)
- Kategorie B: Risiko für Funktionsausfall („funktionskritisch“)
- Kategorie C: Komforteinbuße („Nicht A- oder B-Klasse“; „unkritisch“, früher: „kundenkritisch“)
Fertigung nach dem Stand von Wissenschaft und Technik
Je nachdem, in welche Kategorie eine Schraubstelle eingeordnet wird, ergeben sich für die Prozessfähigkeit der Schraubmontage unterschiedliche Anforderungen. Einfach gesagt, je höher die Kategorie, umso mehr Aufwand muss der Hersteller betreiben, um den Montageprozess abzusichern. Denn im Falle einer Beanstandung muss er nachweisen können, dass er nach dem Stand von Wissenschaft und Technik gefertigt hat – und der ist in Kategorie A ein höherer als in B oder C.
Die wichtigsten Verfahren in der Schraubmontage
Kommen wir nun zu den Montageverfahren, die sich bei Schraubverbindungen etabliert haben:
Mit dem ✚-Zeichen klappen Sie weitere Informationen aus
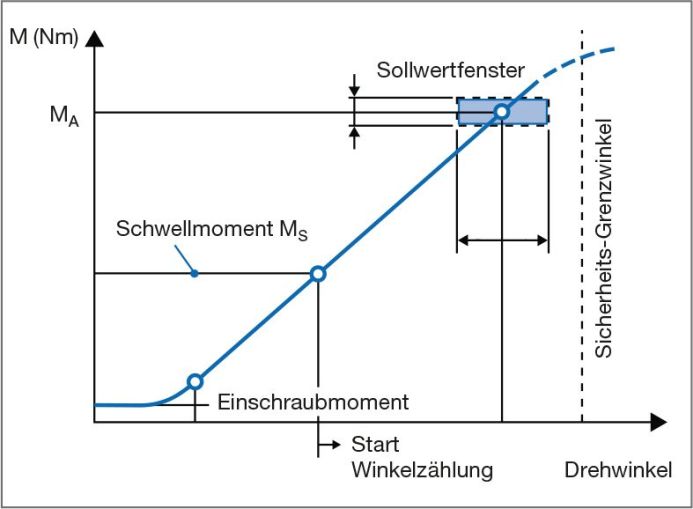
Bild: Böllhoff
Diese Faktoren beeinflussen die Automatisierung
von Schraubmontage-Prozessen
Je größer die Anzahl gleichartiger Schraubstellen in einer Produktion ist, desto eher wird der Betriebsleiter eine Mechanisierung oder (Teil-)Automatisierung in Betracht ziehen. Soll die Montage – effizient – automatisiert werden, sind einige wichtige Voraussetzungen zu beachten. Dazu zählen sowohl auf der Geräteseite als auch bei den Verbindungselementen selbst mehrere Aspekte, darunter:
- Sortierkriterien
- Schraubenantrieb
- Findehilfen
- Verunreinigte Schrauben
- Vibrationswendelförderer
- Verpackung
- Kombi-Elemente
- Verhältnis von Länge der Schraube zu ihrem Durchmesser
Sortierkriterien für Verbindungselemente
Schrauben und andere Verbindungsteile lassen sich innerhalb einer definierten Charge bezüglich verschiedener Kriterien sortieren: Gut- oder Fehlteile, ist das Gewinde vorhanden oder nicht, stimmt der Kopfdurchmesser etc. Ohne besondere qualitätssichernde Maßnahmen kann bei Standard-Verbindungselementen von einer Abweichungsquote bei kritischen Merkmalen von 800 ppm (parts per million) ausgegangen werden.
Das heißt, fast jedes tausendste Teil ist fehlerhaft. Dieses Qualitätsniveau ist für eine vollautomatisierte Schraubenmontage unzureichend. Deshalb empfiehlt es sich, durch spezielle Sortiermaßnahmen sicherzustellen, dass die Komponenten bezüglich der funktionsrelevanten Merkmale einwandfrei sind – zum Beispiel durch eine automatische Kontrolle via Bildverarbeitung. Diese Merkmale müssen zwischen Lieferant und Anwender explizit vereinbart werden.
Die Qualitätszielsetzung „Null Fehler“ ist zum gegenwärtigen Zeitpunkt technisch nicht realisierbar. Durch maschinelle Sortierung lässt sich die Abweichungsquote für einzelne Merkmale jedoch erfahrungsgemäß auf durchschnittlich 10 ppm senken.
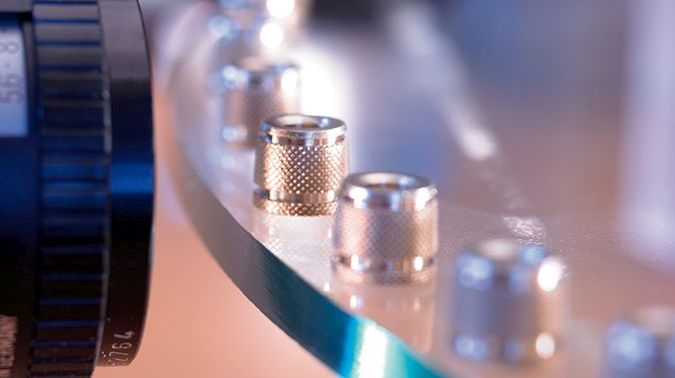
Bild: Böllhoff
Einige Schraubenantriebe können die maschinelle Montage stören
Die Art des Eingriffs des Werkzeugs in den Schraubenantrieb hat einen signifikanten Einfluss auf die Automatisierbarkeit bei der Montage – oder zumindest auf die Störanfälligkeit der automatisierten Prozesse. Das Werkzeug sollte möglichst störungsfrei in den Antrieb (das Schraubenprofil) eingreifen und das Montagedrehmoment zuverlässig übertragen können. Insbesondere sollte der Schrauber-Bit nicht abrutschen, was durch die sogenannte „Cam-out-Kraft“ vor allem bei konischen Schraubprofilen, etwa Schlitz- und Kreuzschlitzprofilen, schnell passieren kann. Die Form des Werkzeugangriffs führt bei der Montage zu einer Axialkraft, die das Werkzeug aus dem Antrieb herausdrücken kann. Dadurch kann sich der Anwender verletzen und das Werkstück beschädigt werden.
Bei zylindrischen Profilen, wie Sechskant oder Innensechsrund (besser bekannt unter dem Markennamen Torx und Torx plus), entsteht diese Kraft nicht. Für hohe Taktraten sind diese Antriebsmerkmale daher deutlich besser geeignet (zum Innensechsrund siehe auch die DIN EN ISO 10664).
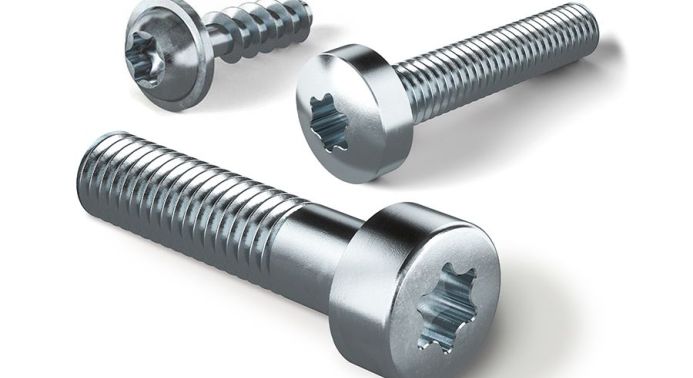
Bild: Böllhoff
Findehilfen vereinfachen das automatische Einfädeln der Schrauben
Speziell bei langen Schrauben oder bei schlecht zugänglichen Schraubstellen kann es von Vorteil sein, wenn das Gewinde am Ende einen Einführzapfen oder ähnliches aufweist. Dies erleichtert das Einfädeln in das Innengewinde und gleicht mögliche Achsversätze aus. Einige Varianten von Gewindeenden sind in der DIN EN ISO 4753 beschrieben. Darüber hinaus gibt es unter den Markennamen Mathread und Navitight weit verbreitete, herstellerspezifische Ausführungen von Findehilfen.
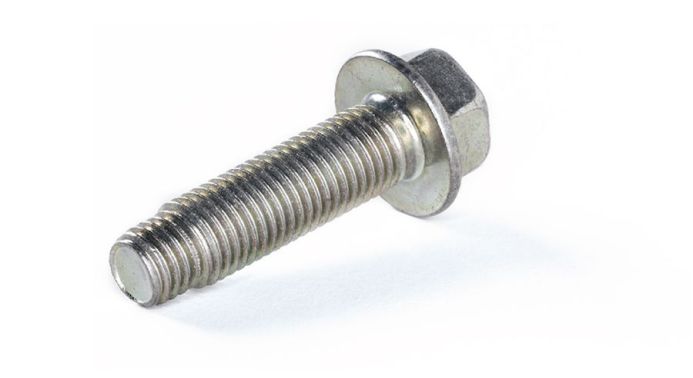
Bild: Böllhoff
Produktionsrückstände auf Schrauben lösen Funktionsstörungen aus
Stahlschrauben, für die kein spezieller Oberflächenüberzug definiert wurde, können mit Spuren aus vorangegangenen Fertigungsschritten verunreinigt sein. Dies ist gemäß DIN ISO 8992 sogar zulässig. Höherfeste Schrauben werden zum Beispiel schlussvergütet; durch diese thermische Behandlung kommt es zu Verzunderungen und Ölablagerung an der Oberfläche. Derartige Rückstände können allerdings automatische Zuführungen und Montageeinrichtungen verschmutzen und Funktionsstörungen auslösen. Deshalb sollte das zulässige Restschmutzniveau für Schrauben in der Massenproduktion möglichst gering sein.
Vibrationswendelförderer beeinträchtigen den Korrosionsschutz
Verbindungselemente aus Stahl werden häufig durch zinkhaltige Oberflächen vor Korrosion geschützt. Werden diese Elemente automatisch zugeführt, kann dieser Prozess den Korrosionsschutz beeinträchtigen. So stoßen die Schrauben zum Beispiel in Vibrationswendelförderern permanent gegeneinander sowie gegen die Wandungen des Fördertopfes, was ihre Oberfläche beschädigen kann.
Für eine automatische Zuführung besonders schlecht geeignet sind Zinklamellenbeschichtungen, da diese Art der Beschichtung nicht so haftfest ist wie es galvanische Schutzschichten sind.
Intelligente Verpackung erleichtert das Handling
Auch die Form der Verpackung ist für einen reibungslosen Ablauf der Montage von Belang. Sie dient primär als Behältnis und Transportmittel, soll aber auch die Beschädigung der Elemente sowie eine Verunreinigung und Vermischung mit Fremdteilen verhindern. Achten Sie für einen geschmeidigen Prozess auf komfortable, schnelle Auspackvorgänge und einfaches Handling. Haben Sie es mit losen, geschütteten Elementen zu tun, die unhandlich oder schlecht zu orientieren sind, so bietet sich eine Bündelung auf einem Gurt („Magazinierung“ der Verbindungselemente) an. Dann dient die Verpackung gleichzeitig als Magazin für das Schraubgerät.
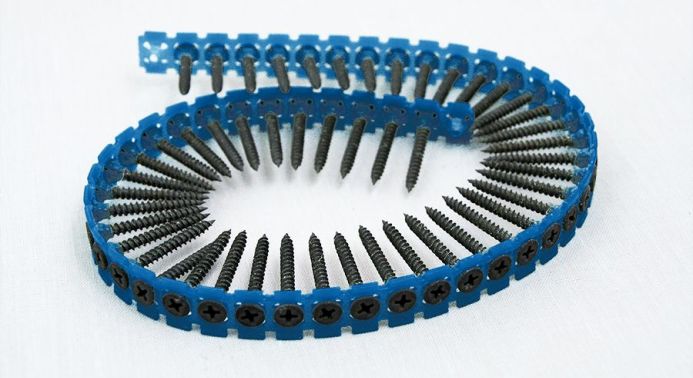
Kombi-Elemente sind wirtschaftlicher
Wenn Verbindungselemente bei der Montage mit Unterlegscheiben kombiniert werden sollen, kann es wirtschaftlicher sein, sogenannte Kombi-Elemente zu verwenden. Dabei werden die Einzelteile schon ab Werk unverlierbar miteinander kombiniert. Somit entfällt der Aufwand des Auffädelns bei der Montage, und die Scheibe kann nicht vergessen oder falsch orientiert werden.
Verhältnis von Länge zu Durchmesser der Schrauben muss stimmen
Sollen Schrauben automatisch bis direkt an die Fügestelle geführt werden, zum Beispiel durch eine Schlauchzuführung, muss die Schraube ihre Orientierung eindeutig beibehalten können. Dazu ist unter anderem ein ausreichendes Verhältnis zwischen Länge und Durchmesser vorteilhaft (Richtwert: Länge > 2 x Durchmesser).
Für die montagegerechte Gestaltung einer Schraubstelle sowie eine effiziente Automatisierung finden Sie im Buch „Technik rund ums Schrauben“ der Böllhoff GmbH weitere hilfreiche Angaben und Tabellen. Ein Exemplar des Buches können Sie hier bestellen.
Die Serie zu Grundlagen der Schraubtechnik im Überblick
Unsere Serie zu den Grundlagen der Schraubtechnik umfasst bislang die folgenden Teile:
- Teil 1: Was ein Konstrukteur über Schrauben, Muttern und Gewinde wissen muss
- Teil 2: Normen, Richtlinien und Auslegung einer Schraubverbindung
- Teil 3: Schrauben – Werkstoffe, Herstellung und Prüfbescheinigungen
- Teil 4: Schraubmontage: Gängige Verfahren und Tipps zur Automatisierung