Wenn Schrauben oder andere Verbindungselemente in der Praxis versagen, liegt es meistens an Korrosion. Dagegen machen zu hohe mechanische Belastungen nur einen geringen Teil der Versagensfälle aus. Daher gilt dem Korrosionsschutz von Verbindungselementen besondere Aufmerksamkeit. Dieser Beitrag erläutert die verschiedenen Arten von Korrosion sowie die Möglichkeiten, Verbindungselemente durch Beschichtungen zu schützen.
Dieser Beitrag basiert auf der 8. Auflage des Buches „Technik rund um Schrauben“, herausgegeben von der Böllhoff GmbH in Bielefeld. Interessenten haben hier die Möglichkeit, sich ein Exemplar des Buches zu bestellen!
Zu den Grundlagen der Schraubtechnik sind in dieser Serie erschienen:
- Teil 1: Was ein Konstrukteur über Schrauben, Muttern und Gewinde wissen muss
- Teil 2: Normen, Richtlinien und Auslegung einer Schraubverbindung
- Teil 3: Schrauben – Werkstoffe, Herstellung und Prüfbescheinigungen
- Teil 4: Schraubmontage: Gängige Verfahren und Tipps zur Automatisierung
- Teil 5: Schraube locker? Nicht, wenn Sie diese Sicherungsmaßnahmen treffen
- Teil 6: Dichtungstechnik: Bohrungen und Wartungsöffnungen sicher abdichten und verschließen
Inhaltsverzeichnis
1. Oberflächenbeschichtungen: Zink opfert sich
2. Korrosionsschutzschichten von Verbindungselementen müssen heute multifunktional sein
3. Neue Chrom-(VI)-freie Beschichtung ist sogar beständiger gegen Rotrost
4. Vorsicht beim Galvanisieren von langen, dünnen Schrauben
5. Welche Metalle sich für eine Beschichtung eignen und worauf man achten sollte
6. Nachbehandlung galvanisch aufgebrachter Zinküberzüge durch Passivierung
7. Zur Gefahr der Wasserstoffversprödung
8. Zinklamellenüberzüge verhindern Versprödung
9. Dünnlackbeschichtungen mit zusätzlichen Schmierstoffen
10. Feuerverzinken: Sehr hoher Korrosionsschutz für größere Schrauben
11. Schichten mit geringerem Korrosionsschutz
12. Gleichmäßige Beschichtung durch chemisches Vernickeln
Korrosion bewirkt an metallischen Werkstoffen eine messbare Veränderung und kann die Funktion des Bauteils oder des ganzen Systems beeinträchtigen. Wenn Schrauben Schaden nehmen, dann fast immer durch Korrosion. Die Verbindungselemente können unter Flächen- und Kontaktkorrosion, Loch-, Spalt- oder Spannungsrisskorrosion leiden (Bild 1). Oder unter allen Arten zusammen.
- Flächenkorrosion ist der gleichmäßige Abtrag der angegriffenen Oberflächen.
- Kontaktkorrosion entsteht durch den Kontakt unterschiedlicher Metalle mit einem Elektrolyten.
- Lochkorrosion tritt an örtlich begrenzten Stellen, zur Beispiel aufgrund beschädigter Schutzschichten auf.
- Spannungsrisskorrosion entsteht unter Einwirkung eines Korrosionsmediums und gleichzeitiger Spannung.
- Spaltkorrosion tritt in Spalten im Werkstoff oder zwischen zusammengefügten Bauteilen auf.
Korrosion entsteht mit der Zeit durch Einwirkung feuchter oder trockener, heißer oder kalter Medien. Sie ist unvermeidlich. Korrosionsschutz ist deshalb als eine Maßnahme zu verstehen, das Fortschreiten der Korrosion zu steuern und zu verzögern.
Verbindungselemente sind Teile eines Korrosionssystems. Um die einzelnen Elemente vor Korrosion zu schützen, muss der Anwender deshalb das System im Gesamtzusammenhang betrachten. Zum Schutz stehen „aktive“ und „passive“ Maßnahmen zur Verfügung: Werden Verbindungselemente aus Werkstoffen eingesetzt, die weitgehend korrosionsbeständig sind, ist dies ein aktiver Korrosionsschutz. Dazu gehören rost- und säurebeständige Stähle oder Nichteisenmetalle. Von passivem Korrosionsschutz spricht man, wenn Verbindungselemente aus Stahl mit einer schützenden Oberfläche versehen werden. Darunter sind alle Arten der Oberflächenbehandlung zu verstehen.
Oberflächenbeschichtungen: Zink opfert sich
Bei den metallischen Schutzschichten unterscheidet man
- anodisch wirkende Oberflächen, zum Beispiel Zink, sowie
- kathodisch wirkende Oberflächen, zum Beispiel Nickel und Chrom.
Zink ist sehr häufig Bestandteil von Schraubenbeschichtungen. Von Vorteil ist, dass das Metall unedler ist als der Stahl des Verbindungselementes: Wird an einem Teil die Zinkschicht beschädigt, dann wird die schadhafte Stelle durch die Reaktion des Zinks wieder geschlossen. Denn durch eine anodische Wirkung „opfert“ sich das Zink für das Stahlteil und löst sich vor dem Grundmetall auf.
Diese Reaktion nutzt man zum Beispiel bei unterirdischen Rohrleitungen und bei Schiffsrümpfen aus Stahl mit Opferanoden. Auch die blanken Gewinde feuerverzinkter Muttern werden durch die Zinkauflage auf den Bolzengewinden geschützt.
Die Oberflächen von Verbindungselementen werden in der Regel elektrolytisch oder galvanisch beschichtet.
Korrosionsschutzschichten von Verbindungselementen
müssen heute multifunktional sein
Wenn Schrauben oder andere Verbindungselemente in der Praxis versagen, ist meistens eine Art der Korrosion schuld. Zu hohe mechanische Belastungen machen dagegen nur einen geringen Teil der Versagensfälle aus. Daher gilt dem Korrosionsschutz von Verbindungselementen besondere Aufmerksamkeit.
Dabei müssen Korrosionsschutzschichten heute weitaus mehr leisten, als „nur“ vor Korrosion zu schützen. Vielmehr sollen sie multifunktional sein und neben dem Design (Farbe, Glanz, Struktur) auch technische Anforderungen erfüllen. Hier ist zu unterscheiden zwischen Anforderungen an die Oberfläche (wie elektrische Leitfähigkeit, Temperaturbeständigkeit oder mechanische Eigenschaften) und an das Applikationsverfahren (zum Beispiel mechanisch, chemisch oder galvanisch).
All diese Anforderungen unter einen Hut zu bringen, war zum Beispiel durch das Verbot von Chrom (VI) insbesondere für die Automobil- und Elektroindustrie eine Herausforderung, der inzwischen jedoch von Zuliefererfirmen wie Galvanotechnikern bewältigt wurde.
Neue Chrom-(VI)-freie Beschichtung ist sogar beständiger gegen Rotrost
Als Ersatz für die Gelbchromatierung bietet zum Beispiel Böllhoff einen neuen Standard, der nach Aussage des Schraubenherstellers hohen technischen Ansprüchen gerecht wird. Es handelt sich bei Verbindungselementen ab der Gewindegröße M5 um eine verzinkte Oberfläche mit einer Schichtdicke von ≥ 5 µm. Darüber hinaus ist diese Oberfläche dickschichtpassiviert, eine Versiegelung optional vorhanden. Die Korrosionsbeständigkeit gegenüber Rotrost ist höher als bei verzinkten, gelb chromatierten Oberflächen. Aufgrund der geringen Schichtdicke kann die neue Oberfläche namens VZD für diverse Schrauben und Zubehörteile genutzt werden.
Vorsicht beim Galvanisieren von langen, dünnen Schrauben
In der Galvanik können die unterschiedlichsten Metalle – nicht nur – auf Verbindungselemente aufgebracht werden. Die häufigsten Überzüge sind Zink, Nickel, Chrom, Kupfer, Messing und Zinn.
Verbindungselemente werden für den Prozess entfettet, gebeizt und auf elektrolytischem Weg in Bädern mit dem Überzugsmetall versehen. Bei Verbindungselementen und Kleinteilen geschieht das überwiegend in Trommelanlagen. Große Verbindungselemente und sperrige Teile werden als Gestellware galvanisiert, um Beschädigungen durch das hohe Eigengewicht zu vermeiden.
Das Metall wird auf der Stahloberfläche nicht gleichmäßig abgeschieden: Hervorstehende Stellen werden stärker, Vertiefungen und Einkerbungen schwächer beschichtet. Für die Schichtdickenmessung sind deshalb feste Messstellen vorgesehen. Bei langen und dünnen Schrauben können beim Galvanisieren durch die ungleichmäßige Schichtdicke Probleme mit der Lehrenhaltigkeit auftreten.
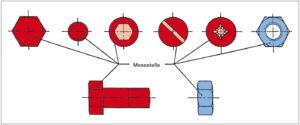
Bild: Böllhoff
Welche Metalle sich für eine Beschichtung eignen
und worauf man achten sollte
- Zink: Das Metall eignet sich wegen der anodischen Wirkung gut für die galvanische Oberflächenbeschichtung, siehe oben. Durch Variation von Galvanisierzeit und Stromstärke kann die Menge des auf dem Verbindungselement abgeschiedenen Zinks und damit die Schichtdicke nach Wunsch bemessen werden. Üblicherweise werden Verbindungselemente mit 5 bis 7 µm verzinkt und passiviert.
- Zinklegierungen: Aufgrund geringer Korrosionsprodukte der Legierungsschicht gewinnen Zinklegierungsschichten an Bedeutung. Die Basis ist immer Zink, versetzt mit anderen Elementen. Nach dem Überzug kann transparent oder schwarz passiviert werden.
- Nickel und Chrom: Im Gegensatz zu den unedlen Metallen wie Zink schützen Nickel und Chrom durch ihre harte Schicht. Diese Metalle sind edler als Stahl. Wenn die Oberfläche verletzt wird, unterrostet das Überzugsmetall und löst sich. Beide Metalle werden zu dekorativen Zwecken eingesetzt. Die Chromoberfläche ist besonders hart, widerstandsfähig gegen Abrieb und läuft nicht an. Chromoberflächen werden üblicherweise nicht direkt auf Stahloberflächen aufgebracht. Stattdessen wird das Stahlteil zunächst verkupfert, dann vernickelt und erst anschließend verchromt.
- Kupfer: Kupferoberflächen dienen als Zwischenschichten für Nickel- und Chromoberflächen und haben eine hohe elektrische Leitfähigkeit.
- Messing: Verbindungselemente werden überwiegend für dekorative Zwecke galvanisch vermessingt.
- Zinn: Teile mit einer Zinnoberfläche lassen sich besser verlöten.
Nachbehandlung galvanisch aufgebrachter Zinküberzüge
durch Passivierung
Bei den galvanisch abgeschiedenen Überzügen ist eine Nachbehandlung zur Verbesserung der Korrosionsbeständigkeit üblich, zum Beispiel eine Passivierung. Passivierungen decken die galvanische Schutzschicht komplett ab und erhöhen dadurch die Korrosionsbeständigkeit. Die Konversionsschichten werden chemisch im Zuge einer Nachtauchlösung aufgebracht. Damit werden auch die Poren der Zinkoberfläche geschlossen.
Gängig sind die (Chrom-VI-frei erhältlichen) Dünn- und Dickschichtpassivierungen sowie die Chromatierung. Im Nachgang kann noch eine Versiegelung vorgenommen werden. Dies geschieht zumeist mit silikathaltigen Substanzen, die mit der Passivierung vernetzt werden. Die Versiegelungen festigen die Optik der Passivierungsschichten, erhöhen den Korrosionsschutz und können eine Reibwerteinstellung übernehmen.
Zur Gefahr der Wasserstoffversprödung
Wasserstoffinduzierter Sprödbruch ist eine Gefahr speziell für Verbindungselemente. Durch das Zusammenwirken von atomar aufgenommenem Wasserstoff und Zugeigen- oder Zuglastspannungen können Bauteile versagen. Bei Zubehörteilen mit federnden Eigenschaften und mit Härten größer 400 HV ist eine erhöhte Sprödbruchgefahr gegeben.
Der Wasserstoff kann beim Beizen, beim Galvanisieren und bei Korrosion aufgenommen werden. Die Empfindlichkeit gegen Wasserstoffversprödung steigt mit zunehmender Festigkeit des Stahls. In Bezug auf Werkstoffauswahl, Wärme- und Oberflächenbehandlung sind daher besondere Maßnahmen erforderlich. Auch bei anderen mechanischen Verbindungselementen kann eine Wasserstoffversprödung auftreten. Sollte diese Gefahr erkennbar sein, sind geeignete Maßnahmen zu treffen, um eine Versprödung zu vermeiden.
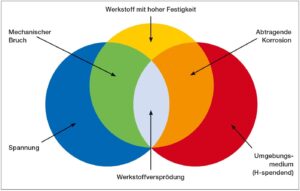
Bild: Böllhoff
Es ist zu beachten, dass Schrauben nicht gefahrlos nachträglich galvanisch oberflächenbehandelt werden können, sofern sie hinsichtlich Werkstoff und Anlasstemperatur nur diejenigen Mindestanforderungen erfüllen, die für die Festigkeitsklassen 10.9 und 12.9 in DIN ISO 898 Teil 1 festgelegt sind.
Zinklamellenüberzüge verhindern Versprödung
Die Gefahr einer Wasserstoffversprödung lässt sich durch einen zusätzlichen Beschichtungsablauf ausschließen. Dabei werden die betreffenden Teile nach dem Reinigen und Entfetten der Oberfläche in eine wässrige oder lösemittelhaltige, dispersive Lösung mit einer Mischung aus Zink- und Aluminiumlamellen getaucht. Anschließend werden sie geschleudert, um das überflüssige Überzugsmetall zu entfernen. Bei großen und sperrigen Teilen wird die Oberfläche aufgespritzt. Zinklamellenüberzüge sind auch als „Dünnbeschichtungen“ oder „Dispersionsüberzüge“ geläufig.
Dünnlackbeschichtungen mit zusätzlichen Schmierstoffen
Topcoats sind Deckbeschichtungen aus einer organischen Verbindung, die in flüssigem Zustand aufgebracht werden. Die Verbindungselemente werden getaucht, oder der Topcoat wird aufgespritzt. Anschließend werden die Teile auf 200 °C erwärmt. Dabei härtet die Lackschicht aus.
Diese Schutzschicht kann in vielen Farben auf eine andere Oberflächenbeschichtung aufgetragen werden. Außerdem können Schmierstoffe in die Schutzschicht eingearbeitet werden, um für die Verschraubung günstige, konstante Reibungszahlen zu erbringen.
Feuerverzinken: Sehr hoher Korrosionsschutz für größere Schrauben
Das thermische Verzinken erfolgt in einem Bad aus flüssigem Zink mit einer Temperatur von circa 500 °C. Durch die hohe Temperatur reagieren Zink und Eisen und bilden eine Schicht aus einer Zink-Eisen-Legierung, die bei der Verarbeitung nicht beschädigt wird. Nach dem Tauchen werden die Verbindungselemente durch Schleudern vom überflüssigen Zink befreit. Die Bolzengewinde dürfen nicht nachgeschnitten werden.
DIN EN ISO 10684 schreibt für feuerverzinkte Teile eine Schichtdicke von mindestens 40 µm vor. Diese dicke Schutzschicht und die darunter liegende Zink-Eisen-Schicht schützen zusammen sehr gut vor Korrosion. Die starke Auflage muss bei der Gewindegestaltung berücksichtigt werden, wenn die Gewinde im verzinkten Zustand schraubbar bleiben sollen. Das Schraubengewinde muss also vor dem Verzinken mit einem stärkeren Untermaß gefertigt werden. Dadurch reduziert sich aber der Spannungsquerschnitt, und die Flankenüberdeckung ist vermindert. Deshalb gelten für feuerverzinkte Schrauben andere Prüfkräfte als für Teile mit galvanischen Beschichtungen (ebenfalls gemäß DIN EN ISO 10684).
Aus den vorgenannten Gründen ist es nicht sinnvoll, Schrauben unter M 8 feuerzuverzinken. Mutterngewinde werden erst nach dem Feuerverzinken geschnitten, sind also nicht verzinkt. Durch das Zink auf dem Bolzengewinde wird auch das Mutterngewinde geschützt.
Schichten mit geringerem Korrosionsschutz
- Phosphatieren oder Bondern liefert einen dunkelgrauen bis schwarzen Oberflächenschutz, der durch das Tauchen in eine Zinkphosphat-Lösung entsteht. Auf dieser Phosphatschicht haften Farbanstriche und Schmiermittel gut. Häufig wird auch phosphatiert, um bei einer Kaltumformung bessere Gleiteigenschaften zu bekommen. Phosphatschichten bieten nur einen geringen Korrosionsschutz.
- Beim Brünieren werden blanke Eisenwerkstoffe bei circa 140 °C in eine oxidierende Lösung getaucht. Es entsteht auf der Oberfläche eine bräunlich-schwarze Eisenoxidschicht. Die brünierten Teile werden anschließend geölt oder gewachst. Der Korrosionsschutz ist sehr gering.
- Das Schwärzen ist ein Verfahren für hochfeste Schrauben. Sie werden bei der Wärmebehandlung nach dem Anlassen in einer Ölemulsion abgekühlt. Das Öl brennt sich in die Oberfläche ein und gibt dem Teil eine schwarze Färbung. Diese Behandlung bietet einen leichten Korrosionsschutz für die Lagerung und den Transport.
Gleichmäßige Beschichtung durch chemisches Vernickeln
Beim chemischen Vernickeln werden die Teile stromlos in einer Nickelsalzlösung beschichtet. Auch an Kanten und in Bohrungen, selbst im Mikrobereich, entstehen sehr gleichmäßige Schichtdicken. Daher eignet sich das Verfahren für kleine und komplizierte Teile. Durch das Überzugsmetall Nickel ist die Oberflächenhärte hoch.