Zu den Grundlagen der Schraubtechnik sind in dieser Serie erschienen:
- Teil 1: Was ein Konstrukteur über Schrauben, Muttern und Gewinde wissen muss
- Teil 2: Normen, Richtlinien und Auslegung einer Schraubverbindung
- Teil 3: Schrauben – Werkstoffe, Herstellung und Prüfbescheinigungen
- Teil 4: Schraubmontage: Gängige Verfahren und Tipps zur Automatisierung
- Teil 5: Schraube locker? Nicht, wenn Sie diese Sicherungsmaßnahmen treffen
- Teil 6: Dichtungstechnik: Bohrungen und Wartungsöffnungen sicher abdichten und verschließen
- Teil 7: Aktiver und passiver Korrosionsschutz für Verbindungselemente
Inhaltsverzeichnis
1. Jeder Werkstoff hat seine Berechtigung
2. Schraubenherstellung: Kaltformen, Gewindewalzen, Vergüten
3. Fokus Oberfläche
4. Konstrukteure achten auf Festigkeit, Anwender auf Belastbarkeit
5. Warmumformung, Gesenkschmieden und spanende Fertigung
6. Für Zugfestigkeit und Streckgrenze: Zehn Festigkeitsklassen für Schrauben
7. Kennzeichnungsregeln für Schrauben und Muttern
8. Belastung bis zur Streckgrenze nur bei geeigneter Kombination von Schraube und Mutter
9. Kennzeichnung von Maßen, Marke oder speziellen Eigenschaften
10. Schrauben und Muttern aus nichtrostenden Stählen sind weniger korrosionsbeständig
11. Werkstoffgruppen, Stahlsorten und Festigkeitsklassen
12. Warmfeste und kaltzähe Stähle für sehr hohe und sehr niedrige Temperaturen
13. Mechanische Eigenschaften durch Zugversuche und Härteprüfungen ermitteln
14. Prüfbescheinigungen nach EN 10204 gelten auch für Schrauben
Schrauben können aus verschiedenen Werkstoffen hergestellt werden. Welches Material gewählt wird, hängt von den Anforderungen an ihre Festigkeit, Korrosionsbeständigkeit und vom späteren Verwendungszweck ab. Im industriellen Bereich eingesetzte Schrauben bestehen vorwiegend aus Stahl, Messing oder anderen Legierungen, Aluminium oder Titan.
Jeder Werkstoff hat seine Berechtigung
-
- Am weitesten verbreitet sind Stahlschrauben. Sie können aus Kohlenstoffstahl, legiertem Stahl oder Edelstahl bestehen. Jeder Werkstoff hat seine Berechtigung: Kohlenstoffstahl ist kostengünstig, legierter Stahl bietet höhere Festigkeit, und Edelstahl ist korrosionsbeständig.
- Messingschrauben bestehen aus einer Kupfer-Zink-Legierung. Sie sind bekannt für ihre gute Korrosionsbeständigkeit und eignen sich besonders für Anwendungen, bei denen elektrische Leitfähigkeit und eine gewisse Ästhetik erforderlich oder gewünscht sind.
- Aluminiumschrauben werden von Konstrukteuren gern dann verwendet, wenn geringes Gewicht erforderlich ist, wie im Flugzeug- oder Automobilbau. Aluminium ist allerdings nicht so fest wie Stahl.
- Schrauben aus Titan dagegen kombinieren beides, hohe Festigkeit und geringes Gewicht. Titan ist leicht und korrosionsbeständig, aber teurer als andere Materialien. In größerem Umfang spielt der Werkstoff daher fast nur im Luft- und Raumfahrtsektor eine nennenswerte Rolle.
Schraubenherstellung: Kaltformen, Gewindewalzen, Vergüten
Schrauben werden in mehreren Schritten hergestellt. Zunächst wird der gewählte Werkstoff in die gewünschte Schraubenform gebracht, und zwar zumeist durch Kalt- oder Warmformen. Die Kaltumformung ist bei Schrauben und Bolzen bis zu einem Schaftdurchmesser von 30 mm und Längen bis 300 mm möglich und üblich. Typischerweise wird dazu Draht- oder Stabmaterial verwendet. Nachdem die Grundform hergestellt wurde, werden die Schraubenköpfe geformt, und zwar durch Stanzen, Fräsen oder Schmieden. Danach folgt das Gewindewalzen, um das Gewinde auf der Schraube zu erzeugen. Bei einzelnen Produkten können spanende Bearbeitungsschritte hinzukommen, um etwa Sechskantschrauben zu entgraten oder um spezielle Kuppen oder Bohrungen anzubringen.
Fokus Oberfläche
Anschließend wird die Schraubenoberfläche bearbeitet, um ihre Festigkeit, Korrosionsbeständigkeit und das Erscheinungsbild zu verbessern. Beispiele für Oberflächenbehandlungen sind das Verzinken, die Beschichtung mit Zink-Nickel-Legierung, das Eloxieren oder das Beschichten mit Polymeren.
Wenn man alle Werkstoffe, Beschichtungen, Gewindetypen und so weiter einbezieht, ergeben sich Trillionen von Kombinationsmöglichkeiten für Verbindungselemente. Wie Konstrukteure sich einen Überblick über Schrauben, Muttern und Gewinde verschaffen, um das optimale Verbindungselement auszuwählen, finden Sie in unserem Beitrag „Was ein Konstrukteur über Schrauben, Muttern und Gewinde wissen muss“ zusammengefasst.
Was ein Konstrukteur über Schrauben, Muttern und Gewinde wissen muss
Konstrukteure achten auf Festigkeit, Anwender auf Belastbarkeit
Für den Konstrukteur ist vor allem die Festigkeit einer Schraube entscheidend, um eine Schraubenverbindung auslegen zu können. Anwender dagegen interessieren sich vor allem für die Belastbarkeit der Verbindungsteile, die wiederum von ihren mechanischen Eigenschaften bestimmt wird. Diese hängen nicht nur vom verwendeten Schraubenwerkstoff ab, sondern auch vom Herstellungsprozess, bei dem sich die Materialeigenschaften verändern können. So hat der Drahtabschnitt des Ausgangsmaterials – gehen wir mal von Stahlschrauben aus – andere Eigenschaften als die fertige Schraube, die nach dem Umformungsprozess noch vergütet (= gehärtet und angelassen) wird. Durch das Vergüten erhält die Stahlschraube eine höhere Zug- und Dauerfestigkeit.
Die Kaltumformung ist die gängigste Herstellungsmethode, da sie zahlreiche Vorteile hat:
- Der Werkstoff verfestigt sich an den umgeformten Zonen,
- die Zugfestigkeit und die Streckgrenze werden erhöht,
- es entsteht eine glatte Oberfläche,
- der Faserverlauf wird nicht unterbrochen,
- Materialfehler werden durch die Umformung sichtbar und
- die Fertigung ist wirtschaftlich.
Auch Sechskantmuttern werden üblicherweise kaltumgeformt. Als Vormaterial dient, wie bei Sechskantschrauben, Draht mit rundem Querschnitt.
Warmumformung, Gesenkschmieden und spanende Fertigung
Wenn die Stückzahlen für den Kaltumformungsprozess zu gering sind oder das Umformverhältnis zu groß ist, dann ist das Warmumformen oder Kopfschmieden eine alternative, weniger aufwendige Herstellungsmöglichkeit. Das eingesetzte Stangenmaterial ist im warmen Zustand stark umformbar, so dass auch kompliziertere Formen gefertigt werden können. Die Oberfläche der Teile ist jedoch verhältnismäßig rau. Warmumgeformt werden vor allem große Durchmesser ab M 30, Überlängen ab 300 mm, komplizierte Formen sowie allgemein kleine Stückzahlen, wie für Kleinserien oder Prototypen.
Weitere Herstellungsverfahren sind das Gesenkschmieden sowie die spanabhebende Fertigung. Beispiele für solche Verbindungselemente sind Rändelschrauben. Auch bei Teilen mit speziellen Konturen, kleinen Radien oder gewünschten scharfen Kanten bietet sich das Verfahren als Herstellungs- oder Nachbearbeitungsmethode an.
Für Zugfestigkeit und Streckgrenze: Zehn Festigkeitsklassen für Schrauben
Während ein Schraubenhersteller den Werkstoff innerhalb bestimmter Normvorgaben auswählt, um die geforderten Eigenschaften bei dem fertigen Teil zu erreichen, orientiert sich der Konstrukteur an der sogenannten „Festigkeitsklasse“, die für seinen Anwendungsfall die richtigen mechanischen Eigenschaften hat.
Für Schrauben aus Stahl sind zehn Festigkeitsklassen definiert, die mit zwei Zahlen bezeichnet werden, die wiederum durch einen Punkt getrennt sind: 3.6, 4.6, 4.8, 5.6, 5.8, 6.8, 8.8, 9.8, 10.9, 12.9. Aus ihnen lassen sich die Zugfestigkeit und die Streckgrenze berechnen. Die Festigkeitsklasse wird auf der Schraube oder Mutter angegeben, um ihre mechanischen Eigenschaften anzuzeigen.
Die erste Zahl steht für 1/100 der Mindestzugfestigkeit. Sie muss also mit 100 multipliziert werden, um die Zugfestigkeit in Newton pro Quadratmillimeter (N/mm2) zu erhalten. Die zweite Zahl muss mit der ersten und dann noch einmal mit 10 multipliziert werden, um die Streckgrenze zu erhalten (oder 0,2 % der Dehngrenze).
Am Beispiel der Festigkeitsklasse 5.6 rechnen wir wie folgt:
- Mindestzugfestigkeit (erste Zahl ist 5) = 5 × 100 N/mm2 = 500 N/mm2
- Streckgrenze = 5 x 6 x 10 N/mm2 = 300 N/mm2
Bis zur Festigkeitsklasse 6.8 wird die Streckgrenze angegeben, ab der Festigkeitsklasse 8.8 die 0,2-%-Dehngrenze.
Kennzeichnungsregeln für Schrauben und Muttern
Für die Kennzeichnungen auf Schrauben und Muttern aus rost- und säurebeständigen Stählen gelten je nach Gewindegröße, Gewindelänge und Belastbarkeit unterschiedliche Regelungen. So werden beispielsweise Sechskantschrauben mit Gewinde ≥ M5 mit voller Belastbarkeit auf der Kopfstirnfläche oder auf der Schlüsselfläche gekennzeichnet, und zwar mit Hersteller, Stahlsorte und Festigkeitsklasse. Solche mit Flansch können wahlweise auf der Kopfstirnfläche oder an der Seite des Kopfes mit den gleichen Angaben versehen werden. Je nachdem, ob aufgrund der Gewindelänge ein Zugversuch möglich ist oder nicht, gelten auch wieder spezielle Kennzeichnungsregeln. So darf bei Gewindelänge b < 3d und nicht möglichem Zugversuch keine Festigkeitsklasse angegeben werden. Ausführliche Informationen zu den mechanischen Eigenschaften von Schrauben aus korrosionsbeständigen Stählen sowie den entsprechenden Kennzeichnungen finden Sie in der DIN EN ISO 3506-1:2020-08.
Belastung bis zur Streckgrenze nur bei geeigneter Kombination von Schraube und Mutter
Bei den Festigkeitsklassen für Muttern aus Stahl wird nur eine Kennzahl angegeben. Diese Zahl gibt etwa 1/100 der Prüfspannung in N/mm2 an. Das entspricht der Mindestzugfestigkeit der dazugehörigen Schraube. Eine Schraube der Festigkeitsklasse 8.8 sollte nur mit einer Mutter der Festigkeitsklasse 8 (oder höher) gepaart werden. Die Schraube kann in dieser Verbindung bis zur Streckgrenze belastet werden. Die entsprechenden Prüfkräfte für Muttern mit Sechskant- oder Regelgewinde sowie allgemein ihre Eigenschaften sind in der DIN EN ISO 4032 festgelegt.
Sechskantmuttern aller Festigkeitsklassen ab Gewindedurchmesser M 5 werden auf der Auflage- oder Schlüsselfläche gekennzeichnet, und zwar im Uhrzeigersinn. Die 12-Uhr-Position wird durch einen Punkt oder das Herstellerzeichen festgelegt, die Festigkeitsklasse durch einen Strich. Muttern mit Nennhöhen ≥ 0,5 D, jedoch 0,8 D, werden mit einer zweistelligen Zahl gekennzeichnet. Diese Muttern sind nur eingeschränkt belastbar. Und Muttern mit Linksgewinde werden mit einem Pfeil auf der Auflagefläche oder mit Kerben am Sechskant gekennzeichnet.
Kennzeichnung von Maßen, Marke oder speziellen Eigenschaften
Die Kennzeichnung der Schrauben (Bild 1) kann neben der Festigkeit auch grundsätzliche Informationen über ihre Eigenschaften und Spezifikationen bereitstellen. So wird bei metrischer Kennzeichnung der Durchmesser der Schraube in Millimetern und das Gewindesteigungsverhältnis angegeben. Eine Schraube mit der Kennzeichnung M8 x 1,25 hat einen Durchmesser von 8 mm und eine Steigung von 1,25 mm pro Gewindegang. In Ländern, in denen zöllige Schrauben verwendet werden, bezieht sich die Kennzeichnung auf den Durchmesser der Schraube in Zoll und die Anzahl der Gewindegänge pro Zoll.
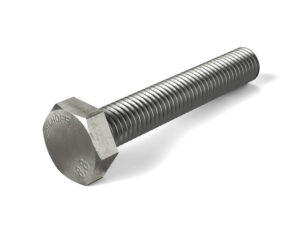
Bild: Böllhoff
Viele Schraubenhersteller kennzeichnen ihre Produkte außerdem mit ihrem Firmennamen oder einer spezifischen Kennzeichnung für ihre Marke. Diese können auf dem Schraubenkopf, dem Gewinde oder der Verpackung angebracht sein. Außerdem können auf den Verbindungselementen weitere spezifische Informationen angegeben werden, zum Beispiel die Art der Beschichtung (verzinkt, phosphatiert) oder sonstige spezielle Eigenschaften (z. B. rostfrei, hitzebeständig).
Schrauben und Muttern aus nichtrostenden Stählen sind weniger korrosionsbeständig
Neben Verbindungselementen aus Stahl mit den Festigkeitsklassen wie 8.8 oder 10.9 werden häufig Schrauben oder Muttern aus nichtrostendem Stahl verwendet. Nichtrostender Stahl – nicht zu verwechseln mit Edelstahl – wird vor allem dann eingesetzt, wenn besondere Anforderungen an die Korrosionsbeständigkeit oder Sauberkeit gestellt werden.
Die Bezeichnung Edelstahl bezieht sich auf die Reinheit des Stahls; rostfrei wird der Werkstoff Stahl dagegen nur dann, wenn er mindestens 10,5 % Chrom in der Legierung enthält. Bei Verbindungselementen aus niedriglegierten Stählen bildet sich auf der Oberflache Eisenoxid: Der Stahl rostet. Zum Schutz vor Korrosion müssen Verbindungselemente aus niedriglegierten Stählen daher in der Regel beschichtet werden. Bei Verbindungselementen aus legierten Stählen, mit einem Chromanteil ab 10,5 %, bildet sich an der Oberfläche Chromoxid. Die dünne Chromoxid-Schicht schützt das Verbindungselement vor Korrosion. Früher wurden Schrauben häufig mit Chrom VI beschichtet; dies ist in der Europäischen Union heute aber bis auf wenige Ausnahmen verboten.
Werkstoffgruppen, Stahlsorten und Festigkeitsklassen
Rostbeständige Schrauben und Muttern werden nach DIN EN ISO 3506 Teil 1 und Teil 2 in Stahl- bzw. Werkstoffgruppen, Stahlsorten und Festigkeitsklassen eingeteilt. Gewindestifte und ähnliche nicht auf Zug beanspruchte Verbindungselemente werden in DIN EN ISO 3506 Teil 3 in Stahlgruppen, Stahlsorten und Härteklassen untergliedert.
Die ISO-Stahlgruppen umfassen vier übergeordnete Werkstoffgruppen (austenitische, ferritische, martensitische und Duplex-Stähle). Diese lassen sich wiederum in eine bis mehrere Stahlsorten und jeweils mehrere Festigkeitsklassen untergliedern:
- Austenitische Chrom-Nickel-Stähle mit einem Legierungsbestandteil von 15 bis 20 % Chrom und 5 bis 15 % Nickel haben eine ausgezeichnete Korrosionsbeständigkeit, gute Duktilität, sind durch Kaltumformung härtbar und relativ gering magnetisierbar. Die Sorten A2 und A4 werden am häufigsten eingesetzt: A2 enthält circa 18 % Chrom und circa 8 % Nickel, ist korrosionsbeständig, aber nicht für salz- und chlorhaltiges Wasser geeignet. Die Stahlsorte A4 hat durch einen 2- bis 3-prozentigen Molybdänanteil eine höhere Korrosions- und Säurebeständigkeit als A2 und eignet sich mit Einschränkungen auch für den Einsatz in salz- und chlorhaltigem Wasser.
- Ferritische Stähle F1 sind durch Kaltumformung härtbar und magnetisch.
- Martensitische Stähle können durch Wärmebehandlung gehärtet werden, haben eine geringe Duktilität und sind magnetisch. Die martensitischen Sorten C1, C2 und C3 weisen normalerweise eine geringere Korrosionsbeständigkeit auf als austenitische Sorten.
- Duplex-Stähle mit einem Mikrogefüge aus austenitischen und ferritischen Phasen haben einen höheren Chrom-Anteil und einen geringeren Nickel-Anteil als austenitische Stähle. Duplex-Stähle sind sehr korrosionsbeständig, können durch Kaltumformung gehärtet werden, weisen eine hohe Festigkeit auf und sind magnetisch.
Warmfeste und kaltzähe Stähle für sehr hohe und sehr niedrige Temperaturen
Für den Einsatz bei sehr hohen und sehr niedrigen Temperaturen (-200 bis +700 °C) müssen Schrauben und Muttern aus sogenannten warmfesten beziehungsweise kaltzähen Stählen verwendet werden. Geeignete Werkstoffe und mechanische Eigenschaften werden in DIN 267 Teil 13 sowie DIN EN 10269 besprochen. Für diese Anwendungsfälle gibt es keine Festigkeitsklassen. Der Konstrukteur legt den Werkstoff fest, der für die Betriebsbedingungen geeignet ist und den technischen Vorschriften entspricht. In jedem Falle muss er berücksichtigen, dass sich die mechanischen Eigenschaften von Schraubenverbindungen bei sehr hohen und sehr niedrigen Temperaturen verändern können. So sinkt zum Beispiel die Zugfestigkeit je nach Festigkeitsklasse und Temperatur auf Werte von 60 bis 95 % der ursprünglich angegebenen Kräfte. Und bestimmte Temperaturen können bei einigen Stahlsorten Versprödungen auslösen. Es ist daher grundsätzlich ratsam, bei besonderen Umgebungsbedingungen den Hersteller der Verbindungselemente hinzuzuziehen.
Mechanische Eigenschaften durch Zugversuche und Härteprüfungen ermitteln
Die mechanischen Eigenschaften von Schrauben werden bei Zug- und Härteprüfungen ermittelt. Beim Zugversuch wird eine Schraube oder ein Probestab auf einer Prüfmaschine (Bild 2) bis zum Bruch belastet. Dabei wird die Schraube in eine Prüfmaschine eingespannt und einer axialen Zugkraft ausgesetzt, bis sie bricht. Die maximale Zugkraft, die die Schraube aushält, wird gemessen und als Zugfestigkeit angegeben. Unter der Belastung wird die Probe erst elastisch länger. Bei Entlastung geht das Teil in die ursprüngliche Länge zurück. Bei einer größeren Belastung dehnt sich die Probe dauerhaft, das Teil wird plastisch verformt. Wird die Belastung weiter erhöht, bricht die Schraube oder der Probestab.
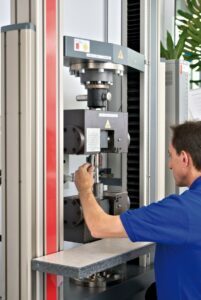
Bild: Böllhoff
Beim Zugversuch (Bild 3) werden folgende Werte ermittelt:
- Die Streckgrenze Re (als Übergang von der elastischen in die plastische Verformung), und zwar als untere und obere Streckgrenze.
- Die Dehngrenze Rp 0,2 für hochfeste Schrauben ab Festigkeitsklasse 8.8. Sie wird anstelle der Streckgrenze gemessen. Es ist auch hier der Übergang von der elastischen in die bleibende (plastische) Verformung bei 0,2 % Längenveränderung zu beachten. Für die Berechnung der Schraubenbelastung ist dieser Wert entscheidend.
- Die Zugfestigkeit Rm der Probe beschreibt ihre höchstmögliche Belastung. Danach lässt der Widerstand nach, und die Probe reißt. Bei Schrauben darf der Bruch nicht unter dem Kopf eintreten, sondern muss im Gewinde oder im Schaft erfolgen.
- Die Bruchdehnung A ist die bleibende Verlängerung in Prozent, bezogen auf die Ausgangslänge. Die Bruchdehnung wird an abgedrehten Probestäben ermittelt.
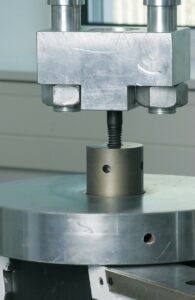
Bild: Böllhoff
Bei der Härteprüfung (Bild 4) wird der Widerstand gemessen, den der Werkstoff einem eingedrückten Prüfkörper entgegensetzt. Die Härte einer Schraube gibt Auskunft über ihre Widerstandsfähigkeit gegen Verformung und Abnutzung. Es gibt verschiedene Methoden, darunter die Rockwell-Härteprüfung, die Brinell-Härteprüfung und die Vickers-Härteprüfung. Bei diesen Verfahren werden Prüfmaschinen verwendet, die den Eindruck oder die Eindringtiefe einer definierten Kugel oder eines Diamanten in die Schraubenoberfläche messen. Der Härtegrad wird dann anhand der Messwerte bestimmt.
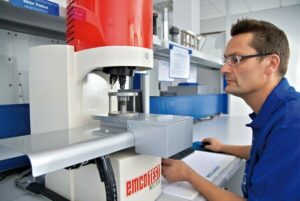
Bild: Böllhoff
Prüfbescheinigungen nach EN 10204 gelten auch für Schrauben
Die EN 10204 beschreibt die verschiedenen Prüfbescheinigungen für metallische Erzeugnisse – und damit auch Schrauben und Muttern, die einem Besteller in Übereinstimmung mit den Vereinbarungen bei der Bestellung vorgelegt werden müssen. Darunter fallen die Werksbescheinigung, das Werkszeugnis sowie zwei Varianten eines Abnahmeprüfzeugnisses („Abnahmeprüfzeugnis 3.1 nach EN 10204:2004“ sowie „Abnahmeprüfzeugnis 3.2 nach EN 10204:2004“).
- In der Werksbescheinigung bestätigt der Hersteller nur die Übereinstimmung mit der Bestellung,
- im Werkszeugnis die Übereinstimmung mit der Bestellung unter Angabe von Ergebnissen einer nichtspezifischen Prüfung.
- Die Abnahmeprüfzeugnisse bestätigen beide die „Übereinstimmung mit der Bestellung unter Angabe von Ergebnissen spezifischer Prüfung“ und unterscheiden sich nur in der Institution, die die Bestätigung erteilt. Im „schwächeren“ Prüfzeugnis 3.1 ist dies ein von der Fertigungsabteilung unabhängiger Abnahmebeauftragter des Herstellers, in der Variante 3.2 ein von der Fertigungsabteilung unabhängiger Abnahmebeauftragter des Herstellers und ein vom Besteller mit der Abnahme Beauftragter oder einer der in den amtlichen Vorschriften genannten Abnahmebeauftragten.
Zu beachten ist, dass die bescheinigten Werte in keiner Prüfbescheinigung „zugesicherte Eigenschaften“ sind! Die Prüfbescheinigungen ersetzen daher keine Wareneingangsprüfung. Die Kosten für die Prüfteile, Prüfungen und Prüfbescheinigungen sind auch nicht im Produktpreis enthalten.