Inhaltsverzeichnis
1. Mehr Flexibilität bei der Herstellung
2. Verschweißfeste Getriebeteile
3. Verschleißfestigkeit gesteigert
4. Vielseitige Fertigungsmöglichkeiten
5. Whitepaper-Tipp
Häufig habe man bei Keramik das spröde Waschbecken oder empfindliches Geschirr im Kopf, „aber wir zeigen interessierten Kunden gerne handfest mit dem Hammer, dass es sich bei unseren Keramiken um widerstandsfähiges Maschinenbaumaterial handelt“, sagt Stefan Veltum, Chief Technology Officer (CTO) der Moeschter Group, zu der unter anderem Doceram gehört.
Einen großen Schritt machte man hier 2020 mit der duktilen Keramik Evocera: Sie kann einen gewissen Teil eingebrachter Verformungsenergie aufnehmen, ohne zu brechen. „Das sind nur wenige Hundertstel Millimeter, was aber in vielen Fällen ausreicht, um eine Anwendung ausfallsicher zu machen“, so Veltum. Denn bis dato sei es für Keramiken nicht möglich gewesen, die Bruchfestigkeit auf den Punkt genau zu berechnen, die statistische Unsicherheit war im Vergleich zu Stahl sehr hoch. Mit Evocera dagegen könne nun per FEM jeder Anwendungsfall sauber simuliert werden. Bei Siliziumnitrid geht man ebenfalls einen Schritt in Richtung bessere mechanische Eigenschaften: Volcera verbindet wenig Gewicht (an Aluminium reicht man nicht ganz heran, Titan allerdings schlägt man deutlich) mit einer geringen Haftung sowie hohen Temperaturschockbeständigkeit und guten Gleiteigenschaften.
Mehr Flexibilität bei der Herstellung
Der fränkische Hersteller MLC hat ebenfalls einen eigenen Werkstoff entwickelt, der die Vorteile von Stahl und Keramik zusammenführt. Der Werkstoff sei im Vergleich zu Stahl robuster, gewichtsreduziert und verschleißbeständiger, lasse sich aber gleichzeitig im Rahmen der Herstellung und Formgebung leichter bearbeiten als herkömmliche Keramik. So sollen die Produktions- und Anschaffungskosten deutlich geringer ausfallen als bei klassischen Hybrid- und Vollkeramiken. „Bei der klassischen Keramikherstellung erfolgt eine aufwändige Produktion durch die eingesetzte Pulvertechnologie, die nur begrenzte Möglichkeiten in der Geometrie- und Formgebung bietet und nachfolgende Sinterprozesse erfordert. Die Grünkörperfertigung wird so zu einem relativ teuren Produktionsschritt, so dass der Einsatz vollkeramischer Bauteile wohl überlegt sein will“, erklärt Michael Schubert, Leiter Produkt- und Prozessentwicklung bei MLC.
Die fränkische Firma stellt den namensgleichen Werkstoff hingegen in einem ersten Schritt aus einem Kunststoff-Grundmaterial her, das mit aktiven und passiven Füllstoffen angereichert wird. Diese Masse kann dann durch bewährte Verfahren, wie etwa Extrusion oder Spritzguss, kostengünstig verarbeitet und in eine erste Vorform gebracht werden. Das polymere Material dient dabei als plastisches Matrixmaterial für die Füllstoffe.
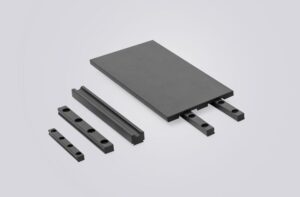
Bild: MLC
Mit Hilfe einer ersten Wärmebehandlung wird die Vorform in einen bearbeitbaren Grünkörper verwandelt. Dieser besitzt eine plexiglasähnliche Beschaffenheit, wodurch ein endkonturnahes Bauteil mit nur geringem maschinellen Aufwand herausgearbeitet werden kann. Durch diese leichte Bearbeitung lassen sich nahezu alle gewünschten Geometrien realisieren und der Werkzeugverschleiß ist im Vergleich zur Bearbeitung anderer Werkstoffe gering. Zum Abschluss wird das Bauteil, das aus dem Grünkörper geformt wurde, in einem Hochtemperaturschritt final gefestigt, wodurch es seine stahlähnliche Härte von 1000 HV bekommt. Dabei wird das Silikonharz vollständig umgesetzt und Rückstände bleiben aus. Für hochgenaue Bauteile kann das keramische Material deshalb ohne großen Aufwand und den Einsatz teurer Werkzeuge wie Diamantschleifer nachbearbeitet werden.
Verschweißfeste Getriebeteile
Auch maxon fertigt in Verfahren, die auf Spritzguss und Extrusion basieren: „Wir sehen zunehmend steigende Nachfragen nach Keramik, da wir immer mehr Anforderungen aus dem Markt erfüllen können“, sagt Stefan Zilm, Business Developer bei maxon. Der Antriebstechnikspezialist hat für eigene Bauelemente die Keramikkompetenz selbst aufgebaut. Inzwischen fertigt man auch für externe Kunden. Die Branche ist überschaubar, da es sich einerseits nachfragetechnisch um eine Nische handelt, gleichzeitig aber viel Know-how erforderlich ist. „Daher hat jeder Hersteller sein eigenes Spezialgebiet etabliert was Prozesse, Materialien, Losgrößen und Toleranzen angeht“, weiß Zilm. Neben bekannten Branchen wie der Medizintechnik beliefert man zunehmend etwa auch Hersteller von hochwertigen Uhrwerken, da Keramikbauteile deren Performance noch erhöhen und damit ein Alleinstellungsmerkmal bieten können: „Durch unsere langjährige Kompetenz in der Herstellung von Getriebe- und Verzahnungsbauteilen für unsere eigenen Produkte konnten wir hier schnell punkten.“
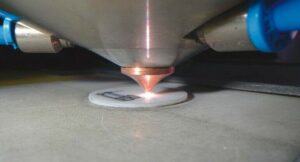
Bild: maxon
Aber auch viele Standardteile wie Buchsen, Wellen oder Düsen können immer öfter aus Keramik gefertigt werden. Denn bei den bisherigen Kritikpunkten Genauigkeit und Preis habe sich laut maxon in den letzten Jahren einiges getan. Dennoch können aber nicht immer alle Wünsche erfüllt werden: Denn nicht jede Toleranz oder Form in Kombination mit Stabilität ist mit jedem Material möglich. Gleichzeitig sei Keramik nicht sofort immer teurer als metallische Werkstoffe. Daher herrsche laut maxon noch größerer Aufklärungsbedarf.
Verschleißfestigkeit gesteigert
Neben Zirkonoxid, das bei maxon in den Motoren vor allem auf Grund seiner Verschleiß- und Gleiteigenschaften gefragt ist, fertigt man auch Produkte aus Aluminiumoxid: Es ist härter, aber mechanisch weniger belastbar und meist als elektrischer Isolator sowie für die gute Wärmeleitfähigkeit gefragt. Daneben erweitern immer öfter auch spezielle Materialien wie Siliziumnitrit das Spektrum, wenn besonders hohe Bruchzähigkeit gefordert ist: In Wendeschneidplatten kommt die Keramik bereits zum Einsatz, es werden aber immer mehr Anwendungsgebiete erschlossen und erforscht, etwa im Motorenbau. Sind dagegen extreme Härte und Temperaturresistenz gefragt, kann Siliziumcarbid die Lösung sein. In der Liste der härtesten Materialien steht es nach Diamant und Borcarbid an dritter Stelle. Bisher kommt diese Keramik vor allem als Läppmittel, etwa zum Polieren von Optiken zum Einsatz. Das Fraunhofer-Institut für Keramische Technologien und Systeme IKTS hat zudem einen keramischen Werkstoff aus Siliziumkarbid und Diamant entwickelt, der die Testverfahren für Verschleißfestigkeit an seine Grenzen brachte: In den bisherigen, zur Vergleichbarkeit fest definierten Zyklenzeiten konnte schlicht kein Verschleiß festgestellt werden. Das Material eignet sich daher für extrem schwer zugängliche Bauteile, wie etwa unter Wasser in Offshore-Anlagen.
„Solche Spezialfälle haben wir dann nicht vollständig im Haus, sondern kaufen beispielsweise Halbzeuge zu und fertigen daraus kundenindividuelle Produkte. So ergänzen sich viele mittelständische Unternehmen gegenseitig“, erklärt Zilm. Entsprechende Partner würden aber zunehmend rarer, was den Einkauf komplizierter mache. Denn größere Konzerne sind an solchen Kooperationen häufig weniger interessiert, sie kaufen stattdessen die Geschäftsbereiche komplett auf: So hat beispielsweise Kyocera im Jahr 2019 die beiden Firmen Friatec und H.C. Starck Ceramics übernommen und schlussendlich als eine Einheit in den Konzern integriert. Die zunehmende Konsolidierung der Keramikbranche zeigt aber auch, dass das Thema immer wichtiger wird.
Vielseitige Fertigungsmöglichkeiten
Neben den reinen Materialwissenschaften hinsichtlich neuer keramischer Werkstoffe werden auch die Fertigungsprozesse immer weiter optimiert. maxon fertigt vor allem mit auf hohe Losgrößen ausgelegten Spritzguss- und Extrusionsanlagen, aber auch Einzelteile und Kleinserien per additivem Verfahren: „Um die Genauigkeit weiter zu verbessern, fahren wir im 3D-Druck auch Parameterstudien bis hinein in den Maschinencode des Herstellers“, so Stefan Zilm. „Bevor das Ganze wirklich vollständig stabil für den breiten Massenmarkt ist, wird es wohl aber noch einige Jahre dauern.“ Denn hochpräzise Bauteile können zwar bereits sehr genau gedruckt werden – theoretisch einzelne Keramikkörner im Mikrometerbereich – was aber sehr lange dauert. Das ist eher für das Prototyping oder spezielle Einzelteile geeignet.
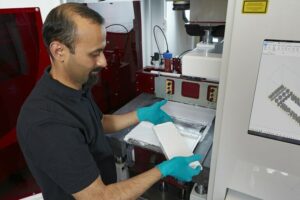
Bild: maxon
Auch die Kombination von verschiedenen Materialien ist additiv inzwischen möglich, wie etwa mit den Maschinen vom AIM3D: Sie drucken eine Verbindung verschiedener Keramiken, aber auch mit Metall oder Kunststoffen, um bestimmte Eigenschaften in einem Bauteil abzubilden. Ebenfalls möglich werden Bauteile, die als volumiger Grundkörper im Spritzguss entstehen und mit einer kleineren Komponente bedruckt werden. Interessant ist auch die Kombination von Keramik zur elektrischen Isolation und Metall für die Leitfähigkeit, was MID-Ansätze (Multi Integrated Devices) ermöglicht.
Die Laserbearbeitung ist eine weitere Möglichkeit, die maxon inzwischen für hochpräzise Keramikbauteile für jährliche Losgrößen von etwa 10.000 in-house etabliert. Da die Prozesse sehr gut automatisierbar seien, könnten damit künftig auch größere Serien gefahren werden. Klassisch spanend wird in der Branche größtenteils der Grünling vor dem Gang in den Sinterofen bearbeitet. maxon entwickelt aber auch immer mehr Verfahren zur Hartbearbeitung, wobei neben dem Schleifen auch spezielle Werkzeuge zum Einsatz kommen. Der Vorteil: Präzision bis in den Mikrometerbereich.
Fraunhofer-Forschende bringen Supraschmierung für Gleitlager in die Anwendung
Auch die Moeschter-Group hat die Anforderung an hohe Präzision im Markt erkannt und in entsprechende konventionelle Bearbeitung investiert. Die eingesetzten Bearbeitungszentren sind für die Serienfertigung im Mikrometer-Bereich geeignet. Bei den additiven Verfahren will man demnächst final entscheiden, welches Verfahren in Dortmund einziehen wird. Entsprechende Experimente und Arbeitsgruppen bestehen bereits seit längerem. „Ein immer größerer Teil unserer Arbeit ist die Systembetrachtung: Denn meist lässt sich nicht einfach ein Stahlteil durch Keramik ersetzen, vielmehr müssen alle Komponenten und Prozesse drum herum ebenfalls in Augenschein genommen werden. Das kann der Kunde durch mangelnde Fachkompetenz selbst meist nicht leisten, weshalb wir das übernehmen“, erklärt Doceram-Vertriebsleiter Carmelo Montalto. Heute sei man häufig gefordert, Innovation auch proaktiv einzubringen – einfach nur Material liefern reiche nicht mehr aus. Teilweise kommen die gleichen Anforderungen von unterschiedlichen Kunden, weshalb man dafür dann bereits einen Standard entwickelt hat. Denn die so durch diverse Projekte aufgebaute Kompetenz bietet Doceram dann auch anderen Firmen an. „Viele kennen die Möglichkeiten nicht, die ihnen offen stehen – weshalb es sich lohne, nachzufragen. So konnten wir etwa schon eine Lösung bieten, die eine Standzeit von acht Wochen auf anderthalb Jahre erweiterte.“
Moeschter-CTO Veltum resümiert abschließend: „Keramik wird in vielen Bereichen wichtiger, der Trend ist klar auch abseits der bisher typischen Einsatzgebiete erkennbar. Es ist aber nicht bei jedem alles zu bekommen, wie es der Konstrukteur häufig von den Metallen gewohnt ist. Für Keramik muss man den richtigen Partner finden.“
Mehr zu Werkstoffen für den Maschinen- und Anlagenbau finden Sie auf unserer Werkstoffseite
Whitepaper-Tipp
Wer sich für den Einsatz von Keramik in technischen Systemen interessiert und wissen will, was konzeptionell mit Blick auf Effizienz und Nachhaltigkeit bei sinnvoller Verwendung möglich ist, findet weitere Tipps in dem Whitepaper ‚Wie ein einzigartiger Werkstoff technische Systeme optimieren kann‘ der maxon motor GmbH. Es enthält Infos zu:
- Was technische Keramik ist und ihre Einsatzmöglichkeiten
- Wann der Einsatz von technischer Keramik sinnvoll ist
- Welche drei Herausforderungen es bei der Konstruktion von technischer Keramik zu beachten gilt
Das Whitepaper lässt sich hier kostenlos herunterladen
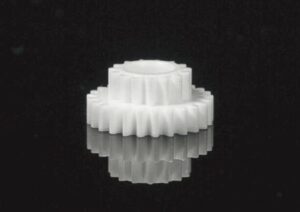
Bild: maxon
Hier finden Sie mehr über: