Voestalpine High Performance Metals (HPM) veröffentlicht eine Fallstudie, die in der Automobilindustrie auf großes Interesse stoßen dürfte: Die Studie des Werkzeugstahl-Spezialisten betrachtet ein Sub-Insert, das im Druckguss-Verfahren zur Produktion von 600.000 Aluminium-Fahrzeugteilen pro Jahr eingesetzt wird. Kann das additiv gefertigte Sub-Insert dem Vergleich mit dem konventionell gefertigten hinsichtlich Temperatur-Beständigkeit, Lebensdauer und CO2-Fußabdruck stand halten?
Megacasting oder Gigacasting liefert großformatige Strukturteile aus Aluminiumdruckguss – das kann schneller und kostengünstiger sein, als dutzende Einzelteile aus Stahlblech zu produzieren und zu fügen. Nicht zuletzt deshalb steht der Druckguss derzeit im Fokus der Automobilindustrie. Das dabei verwendete flüssige Aluminium hat eine Temperatur von 600°C, eine Herausforderung für jeden Werkzeugeinsatz. Voestalpine HPM hat nun ein Sub-Insert entwickelt, das im Vergleich zu einem konventionell gefertigten punktet:
- Laut Studie verlängert sich die Lebensdauer beim gedruckten Bauteil aus dem Hochleistungsmaterial um 150 %.
- Im Fallbeispiel werden auf diese Weise pro Jahr nur noch zehn Sub-Insert-Bauteile benötigt statt wie bisher 25.
- Sollte ein konventionelles Bauteil durch ein solches Produkt ersetzt werden, spare das Bauteil jährlich 66 t CO2-Äquivalente.
- Beim Energieverbrauch werden im Jahr 160 MWh gespart – das entspricht 23.000 Euro weniger an Kosten.
Innerhalb der Fallstudie wurde auch der additive Fertigungsprozess betrachtet. Dieser eröffne im Design und mit seiner Temperaturregelung neue Möglichkeiten für individuelle Produkte: Speziell integrierte Kanäle im Sub-Insert sorgen für eine homogene Kühlung beim Druckgussprozess. Während des additiven Fertigungsprozesses überwachen mehrere Sensoren gleichzeitig die Produktion in Echtzeit und sorgen so für die hohe Qualität des Sub-Inserts.
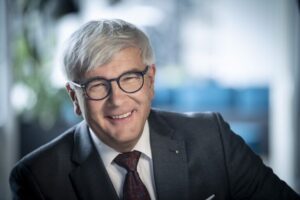
Bild: Christian Jungwirth/Voestalpine
„Die großen Player der Automobilindustrie sind dabei, ihre CO2-Emissionen zunehmend zu reduzieren“. sagt Reinhard Nöbauer, Mitglied des Vorstands der High Performance Metals Division.
„Das hat erhebliche Konsequenzen: Künftig werden die Anforderungen an Produkt-Transparenz beim CO2-Fußabdruck steigen. Wir gehen davon aus, dass die Forderung nach einer Senkung der Emissionen auch die Zulieferer in der Wertschöpfungskette betreffen wird. Deswegen sind Lösungen gefragt, die diese Entwicklung unterstützen – unsere High Perfomance Metals Division bietet solche Lösungen heute schon an und treibt sie gemeinsam mit unseren Kunden voran.“ (eve)