Am wbk – Institut für Produktionstechnik des Karlsruher Instituts für Technologie (KIT) ist es Forschenden gelungen, Endlosfasern innerhalb einer neuentwickelten Laser-Sinteranlage automatisiert in additiv gefertigte Kunststoffteile zu integrieren. Die mit diesem LS-Verfahren hergestellten Bauteile besitzen eine sehr viel höhere Zugfestigkeit als vergleichbare.
Inhaltsverzeichnis
1. Laser-Sinteranlage mit automatisierter Endlosfaserintegration
2. Neues Verfahren hält Einzug in die Praxis
3. Vorteile des Lasersinterns gegenüber anderen 3D-Druck-Verfahren
Endlosfaserverstärkte Faserkunststoffverbunde (eFKV) nehmen in industriellen Anwendungen an Bedeutung zu, wenn es darum geht wirtschaftlich sowie effektiv den Energiebedarf bzw. CO2-Ausstoß von aktuellen sowie zukünftigen Anwendungen in der (Individual-) Mobilität oder im Maschinen- und Anlagenbau zu reduzieren. eFKV bestehen aus einem Polymer, der sogenannten Matrix, und den darin eingebetteten Verstärkungsfasern. eFKV zeichnen sich insbesondere durch ihre hohen mechanischen Eigenschaften bei gleichzeitig geringer Dichte aus. Im Gegensatz zu Bauteilen mit Kurzfasern (Faserlänge ≤= 1 mm) können mithilfe von Endlosfasern (Faserlänge ≥= 50 mm) die mechanischen Eigenschaften von Bauteilen signifikant sowie lastpfadgerecht, d.h. richtungsabhängig, gesteigert werden.
Laser-Sinteranlage mit automatisierter Endlosfaserintegration
Auf Basis einer am wbk neuentwickelten LS-Anlage mit automatisierter Endlosfaserintegration ist es in Zukunft möglich die besonderen Vorteile des LS-Verfahrens mit den Vorteilen der Endlosfaserverstärkung zu kombinieren. Hierfür bewegt sich während des Druckvorgangs in einer vom Nutzer definierten Schicht eine Faserintegrationseinheit über das Baufeld mit den enthaltenen und bereits gefertigten Bauteilschichten. Auf Basis eines NC-Codes (DIN 66025) erfolgt die lineare bzw. nicht-lineare Einbettung von Endlosfaser-Strängen in die Bauteilschichten gemäß den Lastpfad-Informationen im NC-Code. Nach Einbettung sämtlicher Fasern erfolgen das Zudecken der eingebrachten Faserstränge mit Frischpulver und damit das Fortfahren des schichtweisen Aufbauprozesses der LS-Anlage.
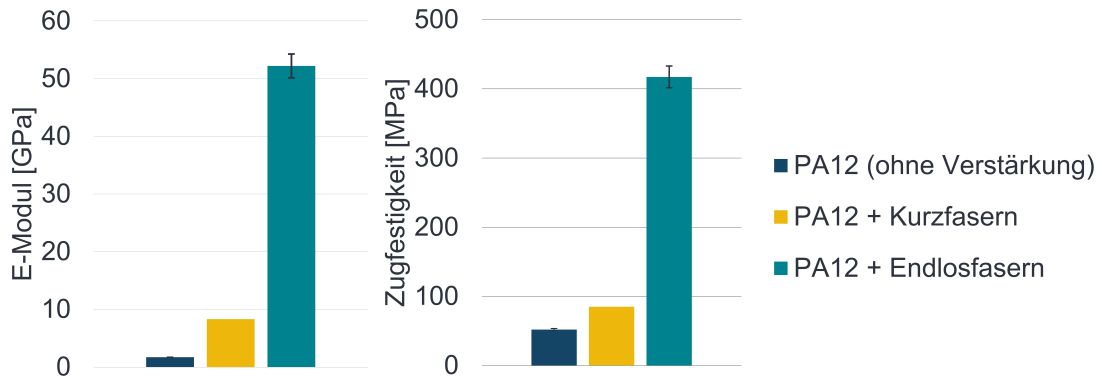
Bild: KIT
Die gemessenen mechanischen Zugeigenschaften (ISO 527) der erzeugten eFKV-Bauteile weisen mit rund 52 Gigapascal ein um das 30,5-fach höheres E-Modul bzw. mit 417 Megapascal eine um die 8-fach höhere Zugfestigkeit im Vergleich zu LS-Bauteilen ohne Verstärkung auf. Aktuell auf dem Markt erhältliche Pulverwerkstoffe aus PA12 mit Kurzfasern (Kohlenstoff) für den LS-Prozess verfügen im Vergleich ein um das 6,2-fach geringeres E-Modul sowie eine um die 6-fach geringe Zugfestigkeit.
Neues Verfahren hält Einzug in die Praxis
Für die durch das Ministerium für Wissenschaft, Forschung und Kunst Baden-Württemberg und dem Bundesministerium für Bildung geförderten Schwesterprojekte „AgiloBat 1“ und „AgiloBat 2“ konnte mit der entwickelten LS-Anlage erfolgreich ein Leichtbaugreifer entwickelt werden. Der Leichtbaugreifer dient zur Handhabung von Batterie-Tabs in einem Ultraschallschweißprozess, der Teil einer Fertigungslinie zur variantenflexiblen Herstellung von Batteriezellen ist. Der so hergestellte Sauggreifer verfügt neben einer integrierten Federfunktion über endlosfaserverstärkte Rippen. Im Vergleich zur konventionell gefertigten Baugruppe konnte damit ein erheblicher Zeit- und Kostenvorteil (keine Werkzeuge oder Zukaufteile wie bspw. Federn) sowie aufgrund der um 80 % geringeren Masse die Belastung für Antriebe verringert werden.
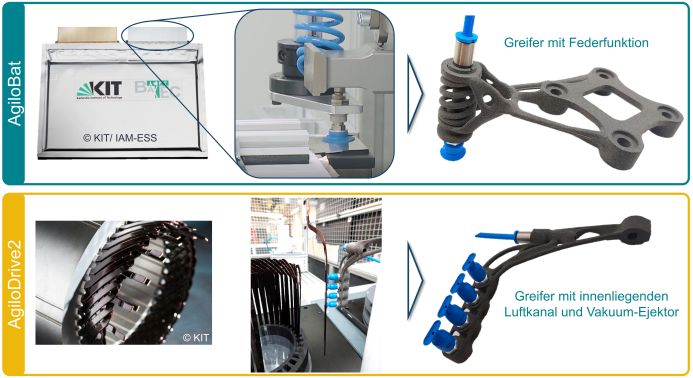
Bild: KIT
Weiterhin wurde für das durch das Bundesministerium für Wirtschaft und Klimaschutz geförderte Projekt AgiloDrive2 ein Sauggreifer für das Handhaben von Hairpins eines Elektromotors mit der entwickelten LS-Anlage umgesetzt. Dieser Sauggreifer verfügt neben innenliegenden Luftkanälen sowie einem integrierten, laser-gesinterten Vakuumejektor (Venturi-Düse) über einen endlosfaserverstärkten Grundkörper. Ebenso wie beim Batterie-Tab-Greifer konnte die Masse um rund 80 %, die Fertigungszeit auf etwa 5 Stunden, die Anzahl der Zukaufteile sowie der manuelle Montageaufwand für den Greifer und damit der Kostenaufwand reduziert werden.
Vorteile des Lasersinterns gegenüber anderen 3D-Druck-Verfahren
Das Laser-Sinterverfahren hat sich in der Industrie in den letzten Jahren eine führende Rolle in der Herstellung von Funktionsbauteilen für Endanwendungen aus Kunststoff erarbeitet. Verantwortlich für diesen stetig wachsenden Erfolg sind die zahlreichen Vorteile dieses Verfahrens gegenüber den anderen additiven Kunststoffverfahren, wie bspw. die Materialextrusion (FLM, FDM, FFF) oder die Vat-Photopolymerisation (SLA, DLP):
- Mit dem Laser-Sinterverfahren können in einem Prozessschritt, d.h. ohne eine zusätzliche Nachbelichtung, robuste Funktionsbauteile mit teilweise höheren mechanischen Eigenschaften wie Spritzgussbauteile aus demselben Werkstoff erreicht werden.
- Zudem fallen Stützstrukturen weg, was eine höhere Designfreiheit ermöglicht. Beim LS-Prozess agiert das unversinterte Pulver als Stützstruktur, wodurch zeit- und kostenintensive Nachbereitungsschritte entfallen. Unversintertes bzw. überschüssiges Pulver kann nach einem Aufbereitungsschritt mit Neupulver vermischt und dem Prozess wieder zugeführt werden.
- Durch die Realisierung von Hinterschnitten, Hohlräumen oder Überhängen können in einem Prozessschritt endkonturfertige Funktionsbauteile oder gesamte Baugruppen ohne nachträglichen Montageaufwand gefertigt werden.
- Weiterhin ermöglicht das LS-Verfahren bei einer hohen Bauraumausnutzung eine wirtschaftliche Einzel- und Kleinserienproduktion, wodurch das LS-Verfahren für einen schnellen Serienanlauf eingesetzt werden kann.
- Im Vergleich zu FLM-Bauteilen besitzen Bauteile aus dem LS-Prozess zudem eine bis zu dreifach geringere Richtungsabhängigkeit (Anisotropie) der mechanischen Eigenschaften, eine höhere Maßhaltigkeit sowie eine geringere Oberflächenrauigkeit.
Damit schafft das LS-Verfahren beste Grundvoraussetzungen für eine wirtschaftliche Herstellung von qualitativ hochwertigen Faserkunststoffverbunden (FKV) mit robusten Grundeigenschaften. (eve)