Inhaltsverzeichnis
1. Bedarf an Kabeln und Leitungen steigt
2. Kürzere Rüstzeiten ermöglichen höhere Varianz
3. Überdimensionierung bei Kabeln und Leitungen senken
4. Digitalisierung in der Herstellung von Kabeln und Leitungen
5. Herausforderung Dekarbonisierung – die Rolle von Kupfer
6. KI-gestützte Suche nach weiteren Lieferanten
7. >Kabelproduktion mit Rohstoffwechsel in nur zehn Minuten
Bedarf an Kabeln und Leitungen steigt
KEM Konstruktion|Automation: Treiben Digitalisierung und die immer weitergehende Elektrifizierung den Bedarf an Kabeln und Leitungen immer weiter nach oben?
Hubertus Breier (Lapp): Kabel transportieren Daten und Strom – sie sind in unserer industrialisierten Welt nahezu unverzichtbar. Und die Nachfrage steigt, vor allem im Bereich der erneuerbaren Energien, der Intralogistik, der Infrastruktur und überall dort, wo digitalisiert wird und die Fabriken smarter werden. Für Lapp bieten sich dadurch große Chancen, aber auch die Herausforderungen in der Produktion wachsen. Zumal dann immer die Frage hinzukommt, welcher Kabeltyp abhängig von Anwendung und Region gefragt ist – woraus sich eine hohe Variantenvielfalt ergibt. Unser Ziel ist es, diese hohe Varianz als Hersteller von Kabeln und Leitungen zu beherrschen, um so Maschinen- und Anlagenbauer immer optimal unterstützen zu können. Als Beispiel seien Windkraftanlagen erwähnt, bei denen es einerseits um die Übertragung von immer höheren Leistungen geht, andererseits aber auch um die Datenkommunikation. Neben klassischen Leitern kommen hier zunehmend optische Kabel zum Einsatz, um den hohen Anforderungen gerecht zu werden.
Kürzere Rüstzeiten ermöglichen höhere Varianz
KEM Konstruktion|Automation: Sie sprachen die hohe Varianz an – ist damit verbunden die Aufgabe, immer kleinere Mengen zu akzeptablen Kosten herzustellen?
Breier: Exakt – die Losgrößen und damit die Kabellängen werden immer kleiner, die Varianten vielfältiger und gleichzeitig wächst der Anspruch, bei Material und Prozessen so nachhaltig wie möglich zu wirtschaften. Gefordert sind also kurze Rüstzeiten – denn lange Rüstzeiten sind eine große Produktivitätsbremse. Zumal es häufig nicht nur um den Wechsel des Querschnitts oder der Aderzahl geht, sondern auch um den Wechsel des Mantelmaterials. Das führt in vielen Fällen dazu, dass erst einmal alles abgeschaltet und abgekühlt werden muss, um eine neue Produktion mit einem anderen Produkt zu starten. Dabei werden das Material und der Extruder ausgetauscht und die Reste entfernt. Dann wird die neue Kabeltrommel eingehängt und das Kabel eingefädelt. Anschließend wird wieder eingeheizt.
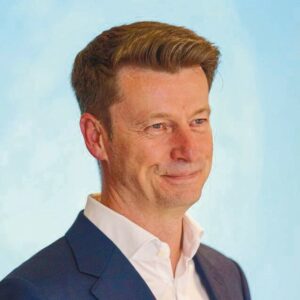
Bild: Lapp
Das ist ein riesiger Aufwand. Wir haben es trotzdem geschafft, die Rüstzeiten auf höchstens 10 Minuten zu reduzieren. Der Trick dabei ist, dass wir in vielen Anlagen bereits zwei Extruder im Einsatz haben – um entweder bei der jeweiligen Produktionsgeschwindigkeit die nötige Menge an Kunststoff bereitzustellen oder etwa bei einem Aderkabel grün und gelb als Coextrusion zu realisieren. Alternativ können wir einen der Extruder nun nutzen, um diesen parallel bereits auf ein neues Material umzustellen – wodurch wir beim Produktwechsel mit minimalem Zeitverzug weiterproduzieren können. Auf diese Weise können wir auch bei kürzeren Kabellängen und vielen Varianten wirtschaftlich arbeiten, ohne hohe Lagerbestände zu schaffen. So arbeiten wir beständig daran, unser weltweites Produktionsnetzwerk zu optimieren, um Effizienz, Lieferfähigkeit und Flexibilität zu steigern.
Überdimensionierung bei Kabeln und Leitungen senken
KEM Konstruktion|Automation: Die Rüstzeiten sind also optimiert – welchen weiteren Herausforderungen muss sich Lapp stellen?
Breier: Neben den Rüstzeiten geht es darum, mit Blick auf Material und Prozesse nachhaltiger zu werden. Bezüglich des Materialeinsatzes ist das eine einfache Rechnung: Wenn die Isolierung eines 10 Millimeter dicken Kabels bei einer Extrusionsgeschwindigkeit von 100 Metern pro Minute 10 Mikrometer dünner würde, könnte pro Stunde über eine Tonne Kunststoff eingespart werden. Dabei muss man wissen, dass ein Kabel heute in vielen Anwendungen oft länger hält als die Maschinen, in denen es eingesetzt wird. Für Verbindungslösungen stellt sich damit die Frage, ob die gleiche Funktionalität mit einigen Prozent weniger Isoliermaterial sichergestellt werden kann. Oder anders formuliert: Können wir es uns in Zukunft noch leisten, Produkte herzustellen, die in diesem Maße überdimensioniert sind? Gefordert sind zudem alternative Designs und Prozesse – auch die jeweiligen Normen für Zertifizierungen müssen dringend überprüft werden, um in der Summe nachhaltiger zu werden.
KEM Konstruktion|Automation: Sind wir denn in der Lage, den Durchmesser um 10 Mikrometer zu reduzieren und sicherzustellen, dass die geforderte Lebensdauer erreicht wird und arbeitet die Fertigungstechnik präzise genug?
Breier: Die Möglichkeiten haben wir! Das erlaubt es uns auch, zwei Zielrichtungen zu verfolgen. Die eine ist, kosteneffizient zu fertigen und einen marktfähigen Preis zu erreichen. Die andere ist die Verpflichtung, den Materialverbrauch zu reduzieren und damit unsere Umwelt besser zu schützen. Auf Basis der hohen Fertigungspräzision und Qualität können wir beide Ziele miteinander verbinden. Deswegen investieren wir in einen Anlagenpark, der in der Lage ist, diese Präzision zu ermöglichen. Und in die Ausbildung unserer Mitarbeiter – nur mit dem Verständnis für die Technik lässt sich diese Präzision auch im Einsatz erreichen. Um Lapp darüber hinaus noch widerstandsfähiger für die Herausforderungen der Zukunft aufzustellen, haben wir zudem drei wichtige Handlungsschwerpunkte definiert – Digitalisierung, Dekarbonisierung und Diversifizierung.
Digitalisierung in der Herstellung von Kabeln und Leitungen
KEM Konstruktion|Automation: Wollen Sie die damit verbundenen Ziele etwas näher erläutern?
Breier: Ziel der Digitalisierung in der Produktion ist, mehr Transparenz im Planungsprozess zu erreichen. Je besser das Portfolio in der gesamten Supply Chain weltweit geplant werden kann, desto besser und effizienter kann die Fertigung erfolgen. Wir beginnen damit oftmals schon beim ersten Kundenkontakt. Mittels Fast-Prototyping entwickeln wir erste physische Muster einfach im 3D-Druck-Verfahren, um Haptik, Optik, Handling sowie Assemblierung in der Produktion und beim Kunden zu verifizieren. Das erleichtert die Abstimmung mit dem Kunden und beschleunigt den Innovationsprozess. Gleichzeitig wird hier die Grundlage gelegt, um alle weiteren Beschaffungs- und Fertigungsprozesse effizient abwickeln zu können. Das gilt in gleicher Weise für Standardprodukte, die sich zum Beispiel auch über unseren Online-Shop konfigurieren lassen.
Herausforderung Dekarbonisierung – die Rolle von Kupfer
KEM Konstruktion|Automation: Wie gehen Sie vor, um die Dekarbonisierung voranzutreiben?
Breier: Eines unserer Hauptziele ist hier, in der Produktion in Richtung eines niedrigeren Verbrauchs von Kupfer zu gehen. Kupfer ist im Durchschnitt für rund 80 Prozent des CO2-Fußabdrucks in den Produkten von Lapp verantwortlich. Daher wird das Thema Recycling strategisch angegangen. Im Werk in Grimaud in Südfrankreich wurden beispielsweise zwei Maschinen gekauft, um den ersten Schritt des Recyclings selbst durchführen zu können. Will heißen, den Mantel von den Leitungen zu ziehen, zu zerkleinern, Kupfer vom Rest zu trennen usw. Das wurde aus einer ökonomischen Betrachtungsweise entschieden und so wird die erste Wertschöpfungsstufe in dem Cradle-to-Cradle-System selbst übernommen. Das Ziel ist natürlich, den ganzen Kreislauf selbst zu besetzen.
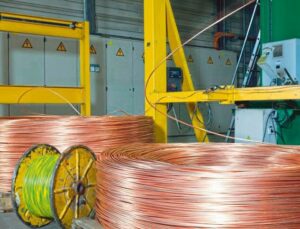
Bild: Lapp
KEM Konstruktion|Automation: Gibt es denn Alternativen zu Kupfer?
Breier: Kupfer ist bis heute der effizienteste Werkstoff, um die elektrische Leitfähigkeit in Leitungen herzustellen. Es bietet den besten Kompromiss aus Preis und elektrischen Eigenschaften. Gold oder Silber leiten ebenfalls gut, sind aber wesentlich teurer – Silber ist zudem sehr oxidationsanfällig. Und Hochspannung lässt sich gut mit Aluminium übertragen – jedes Metall hat seine Stärken. An Kupfer führt aktuell aber kein Weg vorbei. Wir bleiben dennoch wachsam und verfolgen Entwicklungen über unsere Netzwerke in die Wissenschaft.
KI-gestützte Suche nach weiteren Lieferanten
KEM Konstruktion|Automation: Bleibt noch der Punkt der Diversifizierung?
Breier: Hier ist unser Bestreben, in allen Regionen möglichst unabhängig von einzelnen Lieferanten zu werden. Bei der Suche nach neuen Lieferanten setzen wir auch auf eine KI-Lösung. Sie kann in Hochgeschwindigkeit das Internet durchforsten, Lieferanten auf der ganzen Welt finden und sie bewerten. Das ist für uns von Relevanz, da wir an 19 internationalen Standorten in Nordamerika, Asien und Europa fertigen – wir also überall dort sind, wo unsere Kunden sind. Da die meisten Kunden aus Europa stammen, befinden sich dort aktuell auch die meisten Produktionsstandorte, 13 an der Zahl. Jedes Werk setzt aber auch unterschiedliche Schwerpunkte. Im Kabelwerk in Stuttgart werden beispielsweise vor allem Steuerleitungen mit geringerem Volumen und größerer Vielfalt gefertigt. Unser Standort in Monselice in Italien ist auf Datenleitungen spezialisiert, das Werk in Grimaud in Frankreich konzentriert sich auf das Projektgeschäft und die Marine. Die beiden Produktionswerke in Indien (Bangalore und Bhopal) fertigen überwiegend Datenleitungen und Infrastruktur-Kabel und sind eher für große Volumen und große Vielfalt ausgelegt. Korea hat sich auf strahlenvernetzte Leitungen spezialisiert. Und in den USA wird der Fokus auf Steuerleitungen gelegt. (co)
Die von Lapp angebotenen Kabel und Leitungen im Überblick
Kabelproduktion mit Rohstoffwechsel in nur zehn Minuten
In der Câbleries Lapp SARL im französischen Forbach ist die Transformation der Kabelproduktion schon in vollem Gang. Mit einem Strauß an smarten Veränderungen sollen die Produktionskapazitäten bis 2027 verdreifacht werden.
Die Câbleries Lapp in Forbach/Frankreich sind bereits heute das größte Produktionswerk der Lapp Gruppe weltweit. Sie wurden 1990 gegründet. In einer 6000 m2 großen Halle wurden damals 3000 km Kabel pro Monat hergestellt. Das Werk war mit rund 20 einzelnen Artikeln zunächst nur auf Massenproduktion ausgelegt. Heute werden auf 24.000 m2 Hallenfläche pro Monat bis zu 12.000 km Kabel hergestellt. Gleichzeitig ist die Produktion viel anspruchsvoller geworden, denn mit inzwischen rund 2000 Artikeln ist das Produktspektrum deutlich schneller gewachsen als das Volumen, das auch in der Zukunft auf Grund der steigenden Anzahl an kundenspezifischen Produkten immer weiter zunehmen wird.
Ziel ist dennoch, die Produktion bis 2027 zu verdreifachen. Dazu hat das Team um Stéphane Kaczmarek, Senior Vice President der LA EMEA Produktionsgesellschaften und Geschäftsführer der Câbleries Lapp SARL ein ganzes Bündel an Maßnahmen angestoßen oder bereits umgesetzt. Ein wichtiger Baustein ist der Einsatz von neuen, flexibleren Maschinen. So wurde in Forbach in eine neue, fünfte Mantelstraße investiert. Mit ihr verkürzt sich der Rohstoffwechsel beispielsweise von PVC auf PUR von früher 3-4 h auf nur noch 10 min.
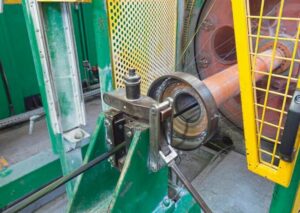
Bild: Lapp
Energie sparen und schneller fertigen
Gemeinsam mit der französischen Firma Komax S.A.S. wurde die neue Mantelstraße nach Vorgaben von Lapp entwickelt. Das Besondere daran: Die Helical-Extruder von Komax benötigen bis zu 25 % weniger Energie, erlauben eine niedrigere Schmelztemperatur und steigern den Ausstoß um bis zu 100 %. Statt eine Stunde lang aufzuheizen, werden nur noch 10 min benötigt. „Wir können damit schneller heizen, schneller reinigen, schneller fahren und sparen noch dazu Energie“, fasst Stéphane Kaczmarek die Vorteile zusammen.
Zukünftig werden auch die vier älteren Mantelstraßen aufgerüstet. Überall wo lange Rüstzeiten die Produktion bremsen, werden gezielt Redundanzen innerhalb einer Linie aufgebaut. So kann die Zwillingsmaschine bereits für den nächsten Einsatz vorbereitet werden, während die erste noch produziert. Diese kann dann schnell ausgetauscht werden, sobald der Produktionsauftrag mit der ersten Maschine fertig ist. Die Rüstzeiten betragen auch hier nur noch 10 Minuten, egal welches Mantelprodukt zum Einsatz kommt.
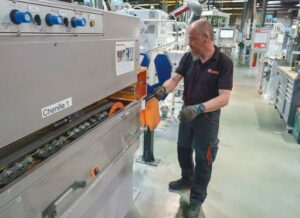
Bild: Lapp
Kürzere Laufwege realisieren
Eine besonders kreative Optimierungsidee hatte das Team bei der Aderstraße. Traditionell ist das Layout einer solchen Produktionslinie in einer Linie aufgebaut. Auf Grund der erhöhten Vielfalt an Artikeln werden aber heute meist nur noch halb so große Produktionslängen verglichen mit vor 10 Jahren gefertigt – die Laufwege für die Mitarbeiter werden damit zu einem Problem, da das Tempo der Maschine reduziert werden muss, um den Wechsel zeitlich zu schaffen.
Zur Optimierung der Laufwege wurde die neue Aderstraße deshalb in U-Form aufgebaut. Dadurch sind die Laufwege um 96 % kürzer, die Umrüstzeiten reduzieren sich von 10 auf 6 min und die Maschine kann fast 50 % schneller produzieren.
Weitere Optimierungsmaßnahmen:
- Für den Transport der Rohstoffe an die Maschinen werden künftig statt Staplern fahrerlose Transportsysteme eingesetzt. Dafür wird auch in ein neues automatisches Hochregallager investiert.
- Eine neue Verzinnungsanlage läuft gerade an.
- Mittelfristig ist die Zentralisierung aller Kunststoffe mit einer automatischen Verteilung an die Extrusionsanlagen geplant.
- An jeder Linie werden außerdem Zerkleinerer zur direkten Wiederverwendung der Kunststoffabfälle installiert.
Hier finden Sie mehr über: